FAQ
Frequently Asked Questions
Heat recovery
Heat recovery contributes to more efficient energy use in your process or factory. This results in lower gas consumption, reduced CO2 emissions and savings on operational costs. It also helps reduce your carbon footprint and meet legal energy-saving obligations, often with attractive payback periods.
The feasibility of heat recovery depends on the residual heat available and the possibilities of reusing it within your process or elsewhere in your factory. Factors such as temperature, flow rate, operational hours, energy prices and internal distances play a role in this regard. Our Heat Recovery Scan provides quick insight into your specific situation and opportunities.
Residual heat can be used more broadly than to heat buildings alone. Think preheating combustion or process air, heating cleaning water or other applications that currently use fossil fuels. During the Heat Recovery Scan, we examine which application offers the most benefit in your situation.
For flue gases with contaminating or corrosive components, it is essential to control cooling properly to prevent condensation and contamination of the heat exchanger. We offer polymer heat exchangers that are resistant to acids and less prone to contamination, enabling heat recovery even with challenging flue gas flows.
The impact on your process is minimal. With our years of experience, we ensure that your installation continues to operate optimally, preferably with a bypass, to keep your primary process undisturbed. We coordinate the execution closely with you to minimise any downtime.
In cooperation with our sister company, we provide a turnkey solution. We work according to a structured approach with four steps: a Heat Recovery Scan, a detailed heat integration design, the actual installation and commissioning, and finally service and maintenance. This ensures that you are completely unburdened and the system performs optimally.
Air preheater
An air preheater (APH) is a gas/ gas heat exchanger that recovers heat from flue gases, baking fumes or drying air to preheat combustion or drying air. Energy is used more efficiently as a result.
Air preheaters are used in thermal combustion and drying processes, such as steam boilers, thermal oil boilers, furnaces and dryers, for preheating combustion and drying air.
Air preheaters increase efficiency, reduce fuel consumption and improve efficiency by 4-10% in combustion and up to 25% in drying, reducing costs and emissions.
In the brick industry, residual heat from kilns is used to preheat combustion air. This reduces gas consumption and significantly increases energy efficiency.
Economiser
An economiser is a gas/liquid heat exchanger that recovers heat from flue gases and uses it to preheat boiler feedwater, process water or thermal oil.
Economisers are used in steam boilers, thermal oil boilers, furnaces and dryers to preheat process water, thermal oil or cleaning water and reduce energy consumption.
An economiser increases energy efficiency, lowers fuel consumption and CO2 emissions and reduces the payback period by making optimal use of residual heat in industrial processes.
In a brewery, residual heat from the steam boiler is used to preheat boiler feedwater, reducing energy consumption and operational costs.
Condensor
A condenser recovers heat from flue gases or drying air and condenses water vapour, reusing both tangible and latent heat in the process.
Condensers are used in steam boilers, dryers, furnaces and thermal oil boilers to preheat process water, boiler feedwater or cleaning water, or to feed heat pumps.
A condenser decreases energy use, reduces CO₂ emissions and utilises condensing heat, leading to higher efficiency and lower operating costs.
In a drying plant, residual heat from exhaust air is utilised to heat process water, resulting in lower energy costs and more efficient heat utilisation.
Roofbox
A Roofbox extracts heat from flue gases via a heat exchanger cartridge, where flue gas releases heat to water. The generated heat can be used directly in operational processes.
The Roofbox is ideal for furnaces and thermal oil boilers in the food, paper and metal sectors, where it reuses heat for process water, cleaning water or to heat a building.
The Roofbox is quick to install, minimises process interruption, integrates easily into existing systems and offers efficient, controllable heat recovery without complex programming.
In a bakery, a Roofbox reuses residual heat from ovens to heat cleaning water, leading to energy savings and lower CO2 emissions.
Our working method
Our work always starts with our Heat Recovery Scan. It serves to map your heat sources and heat users. We then present the most promising heat recovery concepts, with a reliable indication of investment costs, energy and CO2savings and payback time.
Turnkey means we take care of everything: from start to finish. We work closely with our sister company Bos Nieuwerkerk, a specialist in flue gas systems. Together, we can build it all: your heat recovery system, possibly modifying your chimney, an additional duct, a steel structure or a fan that will keep your process conditions unchanged. You have a single point of contact to take care of all the coordination and ensure peace of mind. We monitor the schedule and budget to ensure the project runs smoothly and as agreed.
Depending on the requirements, we manufacture heat exchangers ourselves or in cooperation with our specialist partners. We also produce many components at our own workshop, such as chimneys and flue gas ducts. Our in-house manufacturing is highly appreciated by our clients. When outsourcing manufacturing to our partners, this is always done under the supervision of our engineers.
We believe it is important to keep our promises. Openness and transparency are our top priorities and we only promise what we can deliver. This is exactly why our clients trust and value us.
About Heat Matrix
Heat Matrix was founded almost twenty years ago to enable heat recovery with corrosive flue gases. We succeeded in developing a plastic heat exchanger that was mechanically strong and corrosion-resistant. This opened up a whole new market for heat recovery. And because our clients wanted complete unburdening, we evolved our company into a supplier of turnkey solutions for all types of flue gases.
In terms of technology, design, engineering and implementation, we want to be able to offer our clients everything that is both possible and proven with the current state of the art. In addition, our philosophy is: business is business, but above all, business is people. We put people at the heart of everything we do. We believe in fair, equal business and honouring agreements.
Yes, we have been working for years with trusted partners who, like us, strive to provide industrial companies with the best products. We look for partners who not only deliver quality, but also contribute to our clients’ sustainability ambitions.
BN/HM Groep combines the knowledge and experience of Heat Matrix and Bos Nieuwerkerk to realise turnkey flue gas systems and heat recovery solutions. In the future, other companies may join to work together and create a smarter and more sustainable industry.
Careers at Heat Matrix
Working at Heat Matrix and Bos Nieuwerkerk is more than just a job. It is an opportunity to develop yourself in an environment where job satisfaction and cooperation are paramount. We see everyone as a valuable team member and value personal attention.
We invest in our employees by guiding them with education, training and coaching. Whether you are an experienced professional or starting off your career, we offer the space to grow, learn and achieve success together.
Our work process consists of four phases: analysis and advice, engineering, realisation and service. Various specialists work within these steps, such as salespeople, project and process engineers, project managers, work planners, structural engineers, welders and assembly workers. Interested in a position or internship? Take a look at our vacancies or get in touch.
We believe in a culture centred on job satisfaction, collaboration and personal growth. Many colleagues stay with us long-term, which makes for a close-knit team and a strong sense of responsibility.
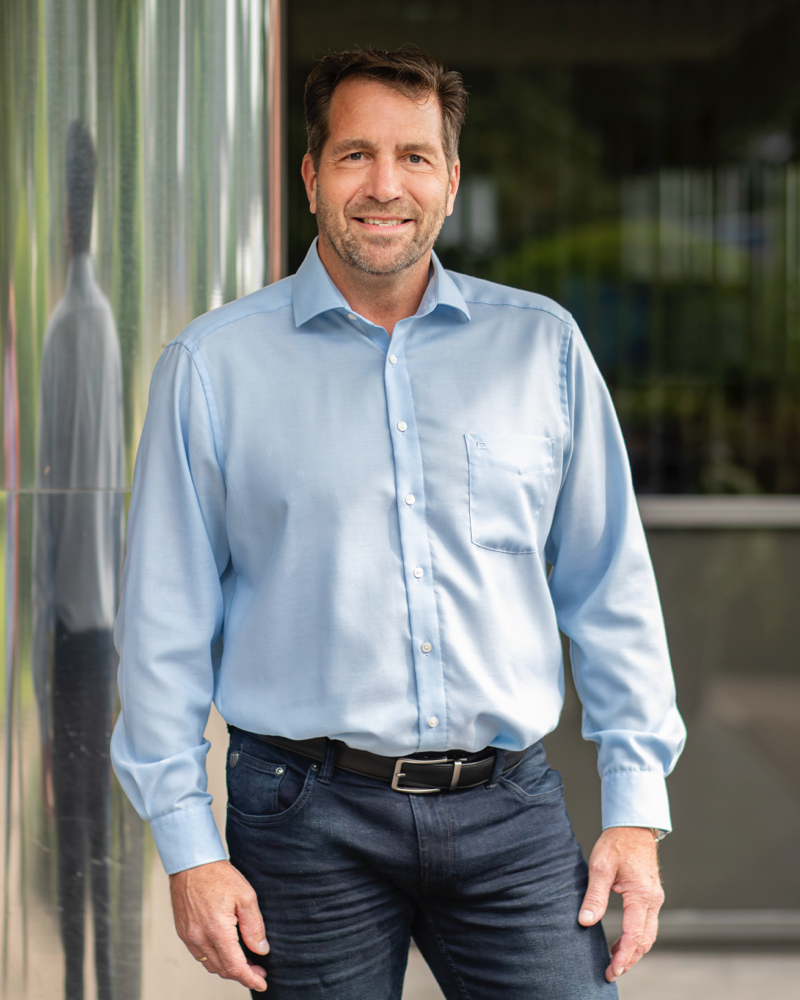
Contact
Samen aan de slag?
Met onze kennis én een no-nonsense aanpak hebben we het antwoord op uw vraag met oog op maakbaarheid, planning en kosten. Neem contact op met Cor de Leeuw.