Heat recovery
Turnkey solutions for Co₂ reduction & energy savings
Up to 30% of industrial heat is lost through flue gases. However, this residual heat can often be reused within the same or a nearby process – reducing CO₂ emissions and energy costs with payback periods typically between 3 and 5 years. Heat Matrix specializes in industrial heat recovery solutions tailored to your sector.
INDUSTRies
In-depth knowledge of diverse industries
With our in-depth knowledge of, and experience with, highly diverse industries, we can guarantee optimal heat recovery. Heat from flue gases, baking fumes or drying air is maximally recovered and integrated into your plant, or used elsewhere in your factory. Together with you, we determine which heat recovery concept is the best match.
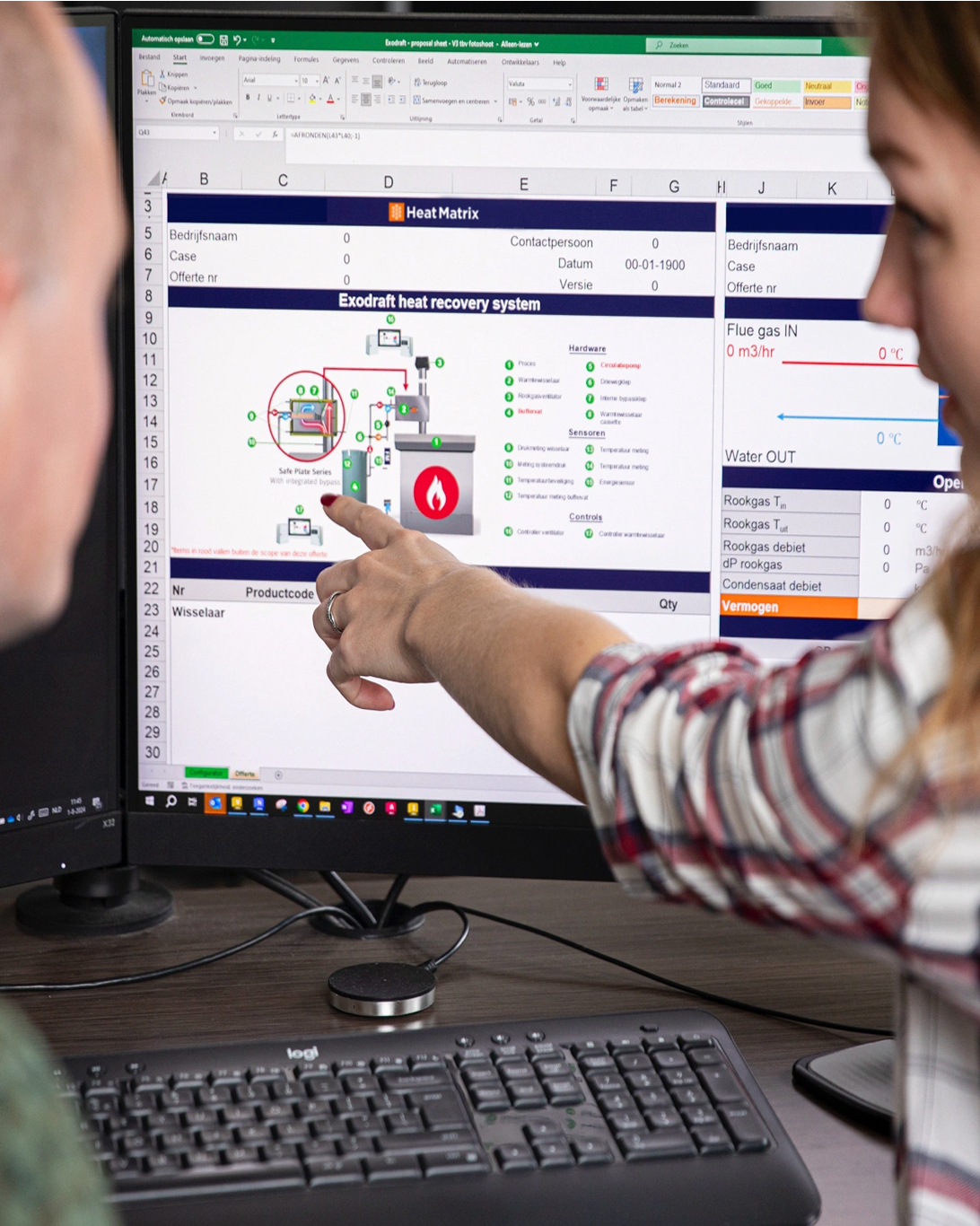
HEAT RECOVERY SCAN
Lightning-fast insight into opportunities, approach and business case
Our work always starts with our Heat Recovery Scan. It serves to map your heat sources and heat users. We then present the most promising heat recovery concepts, with a reliable indication of investment costs, energy and CO2savings and payback time.
TURNKEY
Turnkey means we take care of everything: from start to finish
Heat Matrix works closely with sister company Bos Nieuwerkerk, a specialist in chimneys and flue systems for over 50 years. Our partnership allows us to realise everything we come up with. This means that Heat Matrix provides you with a business case on paper as well as a working installation.
In addition to a report, we deliver complete working installations
Rik Kuenen, Project Engineer
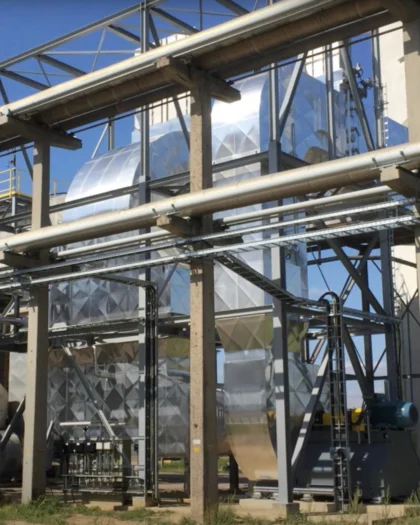
Many flue gas systems discard heat
Do not discard heat! We offer heat recovery solutions that reuse your heat in your primary or secondary process.
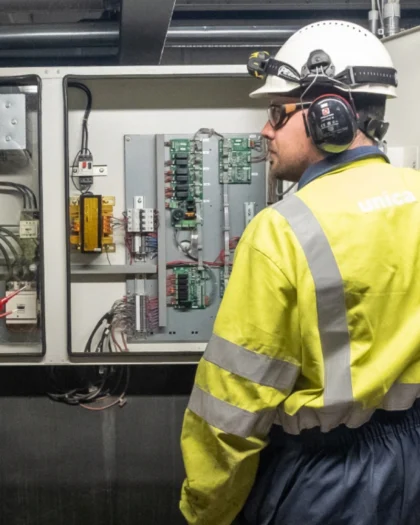
Turnkey or prepared for automation
Together with Unica Industry Solutions, we can fully deliver your heat recovery system, complete with measurement and control technology.
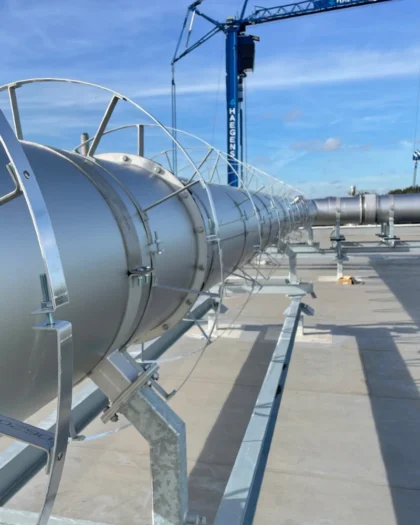
Implementation of all necessary ducts
In our design, we usually opt for a bypass for your heat recovery system requiring additional ductwork. We take care of this for you as well.
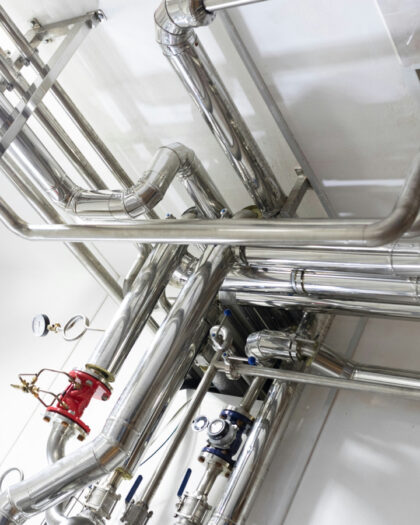
Installation of water pipes included
In many cases, your heat recovery system will also require the installation of water pipes. We will take care of it.
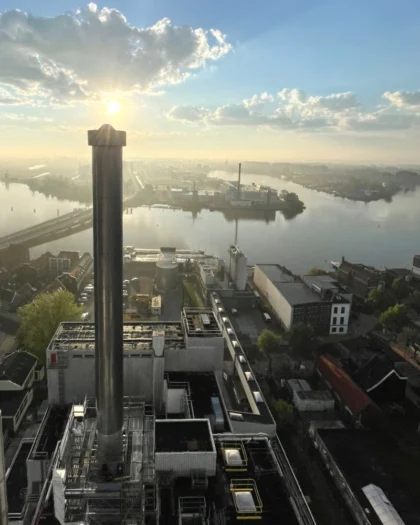
Modifying your chimney
Does your heat recovery system require modifications to your chimney or the installation of additional dampers? Together with our sister company Bos Nieuwerkerk, we will take care of it!
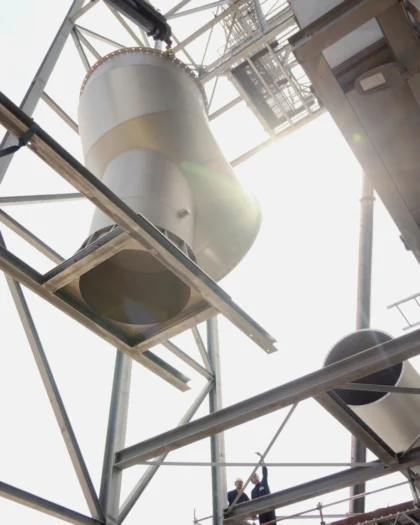
We deliver what is needed for support
A system for heat recovery is often installed at height. This requires support or certain auxiliary structures. We take care of this as well!

Optimal airflow for a stable process
We usually supply our heat recovery systems with a fan, leaving your current process conditions unchanged.
REFERENCES
Savings can be made! Check out our projects to find out
From paper manufacturer to beer brewer, from biscuit to brick manufacturer, we achieved significant savings in energy and CO2 emissions for numerous manufacturers.
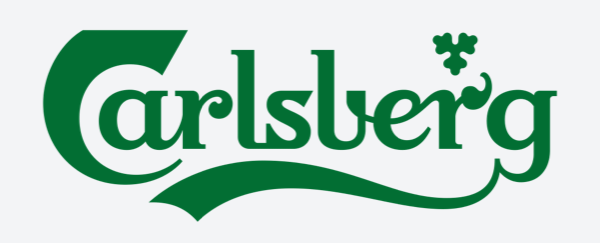
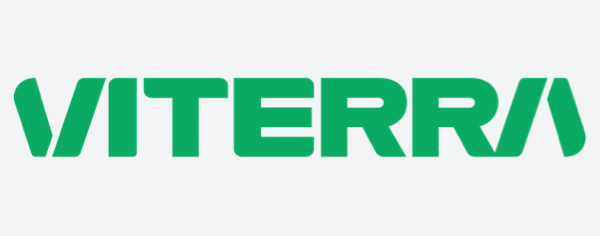
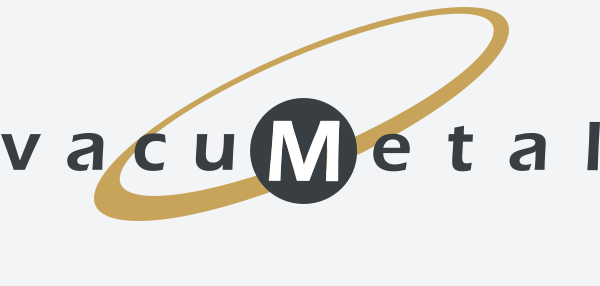
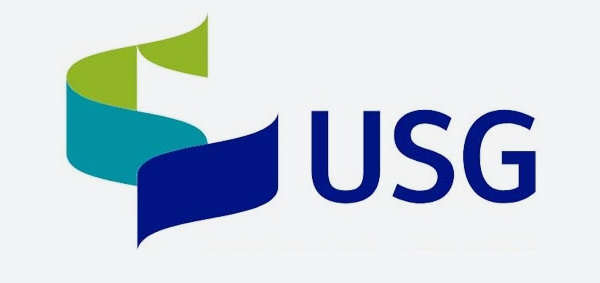
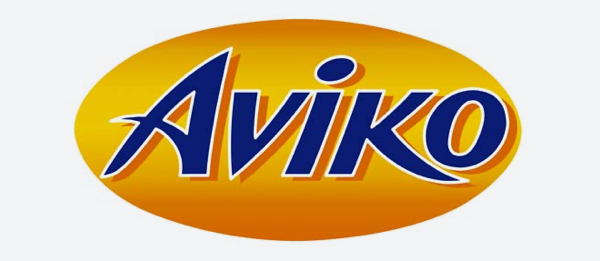
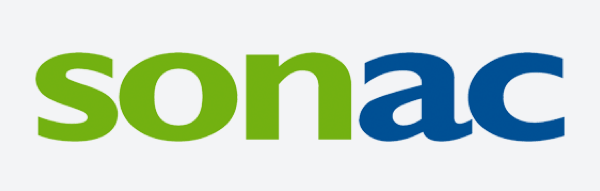
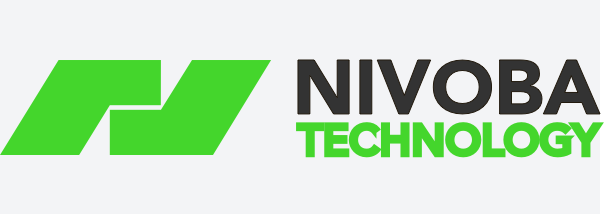
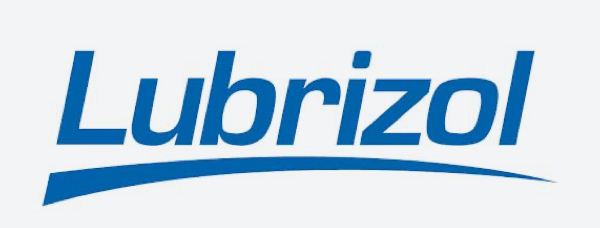
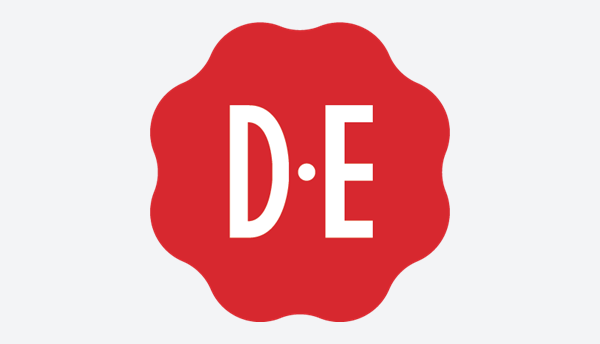
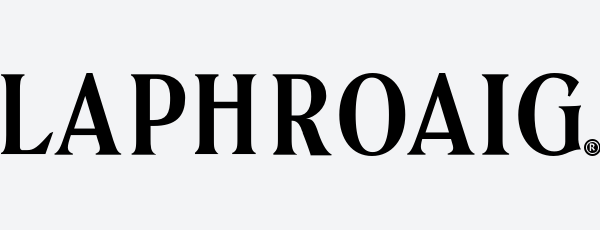
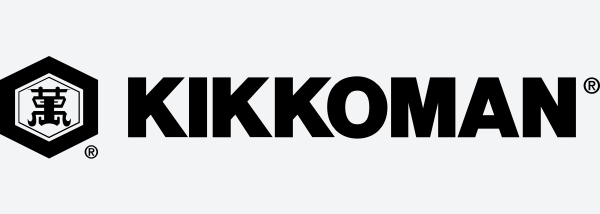
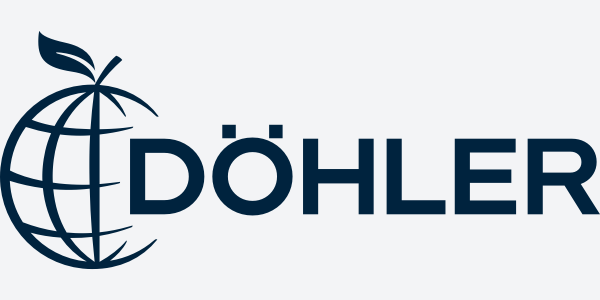
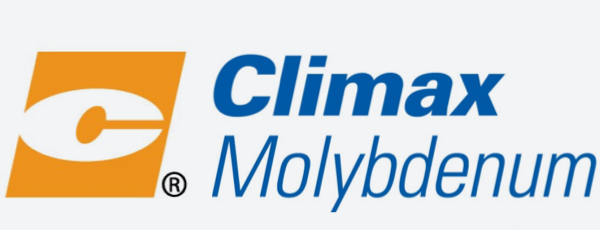
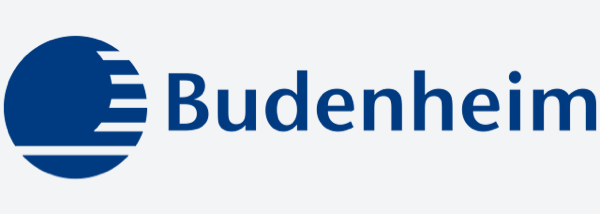
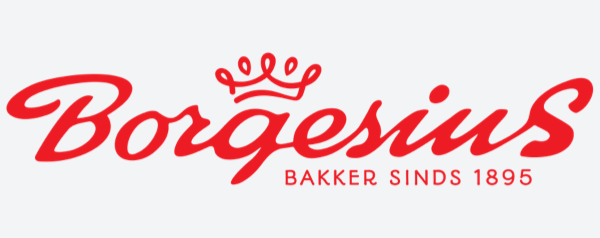
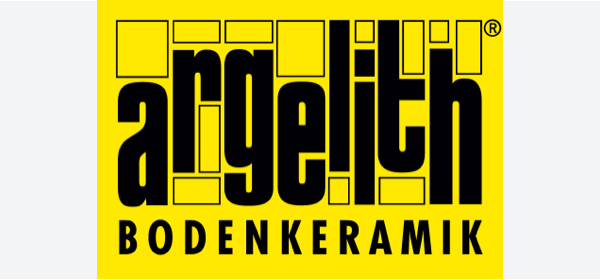
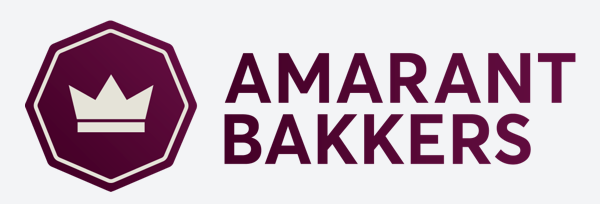
Heat Matrix performance guarantee
- Expertise in industrial processes and heat recovery
- Substantial savings on energy costs and CO2 emissions
- Maximum utilisation of residual heat
- Unburdened project implementation
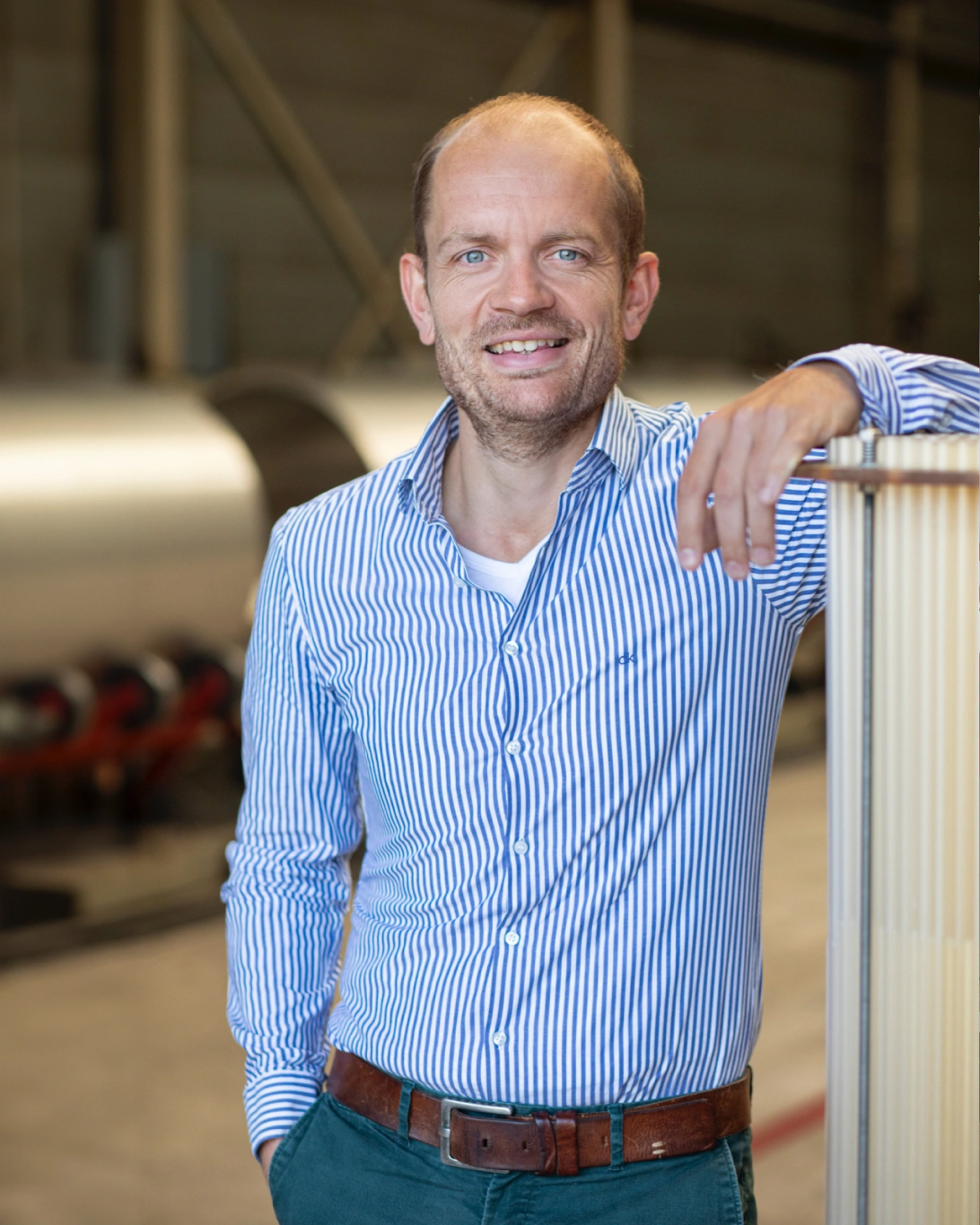
Contact
Curious about your savings potential?
A Heat Recovery Scan gives you quick insight into the most promising concepts for heat recovery, energy savings, reduction of CO2 emissions and payback period.