Bakery industry
Heat recovery for the bakery industry
The opportunities for industrial bakeries to reduce CO2 emissions, cut energy consumption and save money are huge. Because in these sectors, there are two sources of residual heat: flue gases and baking fumes. Heat Matrix will tell you how to put these sources to optimal use. We take into account the fact that the fumes from your ovens may be greasy, sticky or otherwise contain substances that clog ordinary heat exchangers.
So much potential!
Your oven, boiler or thermal oil stove loses up to 20% of the energy you consume through the chimney. Put an end to this waste with heat recover.
Significantly lower your annual energy costs
Structurally reduce your CO2 emissions
Prevent harmful corrosion and contamination
Minimal contamination and two cleaning options
Flue gases from indirectly fired gas ovens are relatively clean. Baking fumes from ovens usually are not. Many fatty ingredients, such as butter and chocolate, are used in biscuit production. This can be overcome with a Roofbox with an interchangeable heat exchanger cartridge. The dirty cartridge is replaced by a clean one, so the dirty one can be cleaned manually.
The Roofbox is a gas-liquid heat exchanger that is easy to install thanks to its modular design. The Roofbox is placed in a skid on the roof. We calculate the roof load in advance. Installation requires only minimal process interruption. Plus, the system is scalable.
How heat recovery works
Capture residual heat …
When hot flue gas or baking fumes leave your chimney, they still contain a significant amount of energy. Our heat recovery system captures this heat from baking ovens, steam boilers or thermal oil heaters.
… And uses it to preheat air or water
The captured residual heat can be used to preheat oven or dryer air, heat cleaning water or heat your buildings. Whichever option you choose, heat recovery directly reduces your fossil fuel consumption!
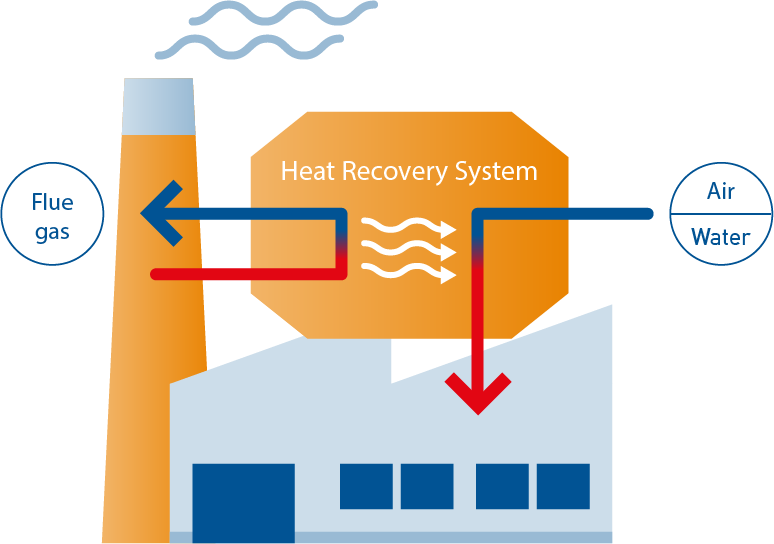
Heat from the oven, to the oven
With the heat we capture from the baking fumes, we can preheat the circulating air for the oven from 15 to 103°C, resulting in a heat recovery of 143 kW and a 20% reduction in the gas consumption of your oven. An alternative way of utilising residual heat from flue gas or baking fumes is by heating water for use in (crate) washing machines, dough preparation or to heat the building.
We realise energy savings for the following production processes
- Bread
- Pastry
- Snacks
- Frozen foods
- Raw and semi-finished bakery products
We recover heat from the following thermal processes
- Baking ovens: Up to 20% of the heat from baking ovens is lost through the chimney. This heat from hot baking fumes and flue gases can be used to preheat air or water.
- Steam boilers: Hot flue gas from steam boilers leaving the chimney still contains more than 10% of the energy your process requires. It can be recovered and used for preheating combustion air, boiler feedwater or cleaning water.
- Thermal oil heaters: In thermal oil stoves, 8-15% of the energy is lost through the chimney. It can be recovered and used to preheat combustion air or water for cleaning and heating buildings.
SOLUTIONS
Heat exchangers for the bakery industry
For residual heat recovery, we use heat exchangers that transfer residual heat to cold air streams (gas/gas heat exchangers) or heat exchangers that transfer residual heat to cold water or thermal oil (gas/liquid heat exchangers). The composition of the flue gas determines what material the heat exchanger is made of: metal or polymers. For corrosive or highly polluting flue gas, we opt for a polymer heat exchanger.
Our three clear promises
Gain insight into costs and benefits in advance
We deliver corrosion and contamination-resistant systems
Payback periods of 3 to 5 years are feasible
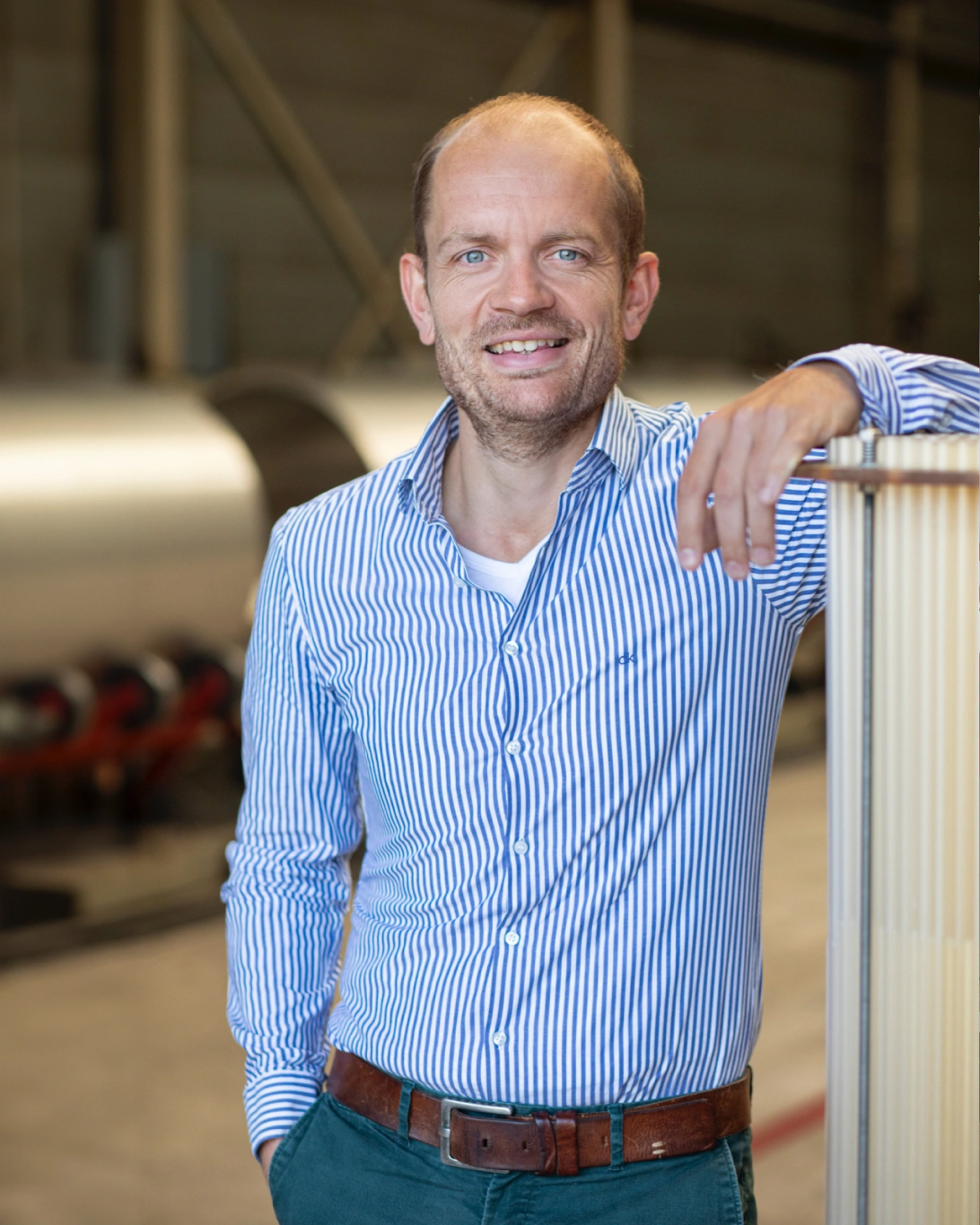
Contact
Curious about your savings potential?
A Heat Recovery Scan gives you quick insight into the most promising concepts for heat recovery, energy savings, reduction of CO2 emissions and payback period.