Chemical industry
Heat recovery for the chemical industry
In the food and beverage industry, heat recovery possibilities tend to be limited by corrosion and contamination. We put an end to that limitation with corrosion and dirt-resistant heat recovery systems that harness your residual heat for your primary or secondary processes.
So much potential!
The sooner you deploy heat recovery, the faster you will start earning with this investment.
Significantly lower your annual energy costs
Structurally reduce your CO2 emissions
Prevent harmful corrosion and contamination
The non-ferrous metal market
The non-ferrous metal market produces metals from ores. To remove impurities such as sulphides from the ore, the ore is roasted. This creates a flue gas stream with a temperature of 250⁰C and a high SO2 concentration. This highly corrosive flue gas is usually extinguished with water. A great loss of energy that Heat Matrix can put back to work for you.
Drying processes
The efficiency of a dryer can be improved by up to 20% by using a polymer air preheater or economiser. Every 1% efficiency improvement of your dryer directly results in 1% reduction of your CO2 emissions. We use the extra recovered residual heat to heat the air entering the dryer, or the process water.
Petcoke
Petcoke, a residue from oil refining, is a raw material for TiO2 production and anode production for the aluminium industry, among other things. Both industries have flue gas treatment systems with high flue gas temperatures. The sulphur components in petcoke lead to corrosive flue gases. Incinerators and RTOs are used to rid the flue gas of volatile organic compounds (VOCs). HeatMatrix can recover heat from flue gases. In TiO2 production, this residual heat can be used to heat the boiler feedwater. In anode production, the heat can be fed to the anode baking furnace.
Household chemicals
A number of thermal processes take place in a chemical plant, such as in fired heaters, steam boilers, thermal oil heaters, dryers, furnaces and other installations. Up to 15% of the primary energy consumed is lost through the chimney. The heat from flue gas can be recovered and fed to the furnace or dryer. This achieves a significant reduction in energy consumption and CO2 emissions. Alternatively, the residual heat can be used to heat boiler feed or process water.
How heat recovery works
Capture residual heat …
When hot flue gases or exhaust air from your dryer leave the process chimney, they still contain a significant amount of energy. Our heat recovery system captures this heat from your plant.
… And uses it to preheat air or water
The captured residual heat is used to preheat the air for your furnace or dryer. Your buildings can be heated with this residual heat as well. The result is an immediate drop in your fossil fuel consumption!
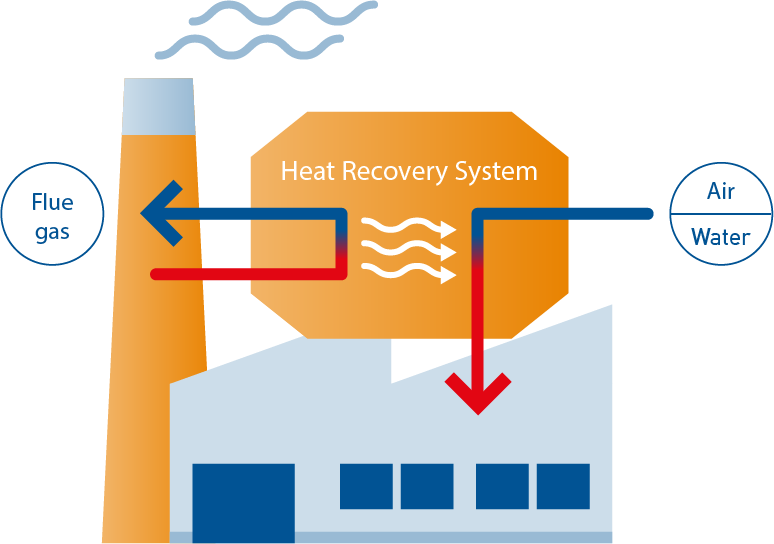
SOLUTIONS
Heat exchangers for the chemical industry
For residual heat recovery, we use heat exchangers that transfer residual heat to cold air streams (gas/gas heat exchangers) or heat exchangers that transfer residual heat to cold water or thermal oil (gas/liquid heat exchangers). The composition of the flue gas determines what material the heat exchanger is made of: metal or polymers. For corrosive or highly polluting flue gas, we opt for a polymer heat exchanger.
Our three clear promises
Gain insight into costs and benefits in advance
We deliver corrosion and contamination-resistant systems
Payback periods of 3 to 5 years are feasible
Heat Matrix guarantees
- Expertise in industrial processes and heat integration
- Substantial savings on CO2 emissions and energy costs
- Maximum utilisation of residual heat
- Insight into performance in advance and in hindsight
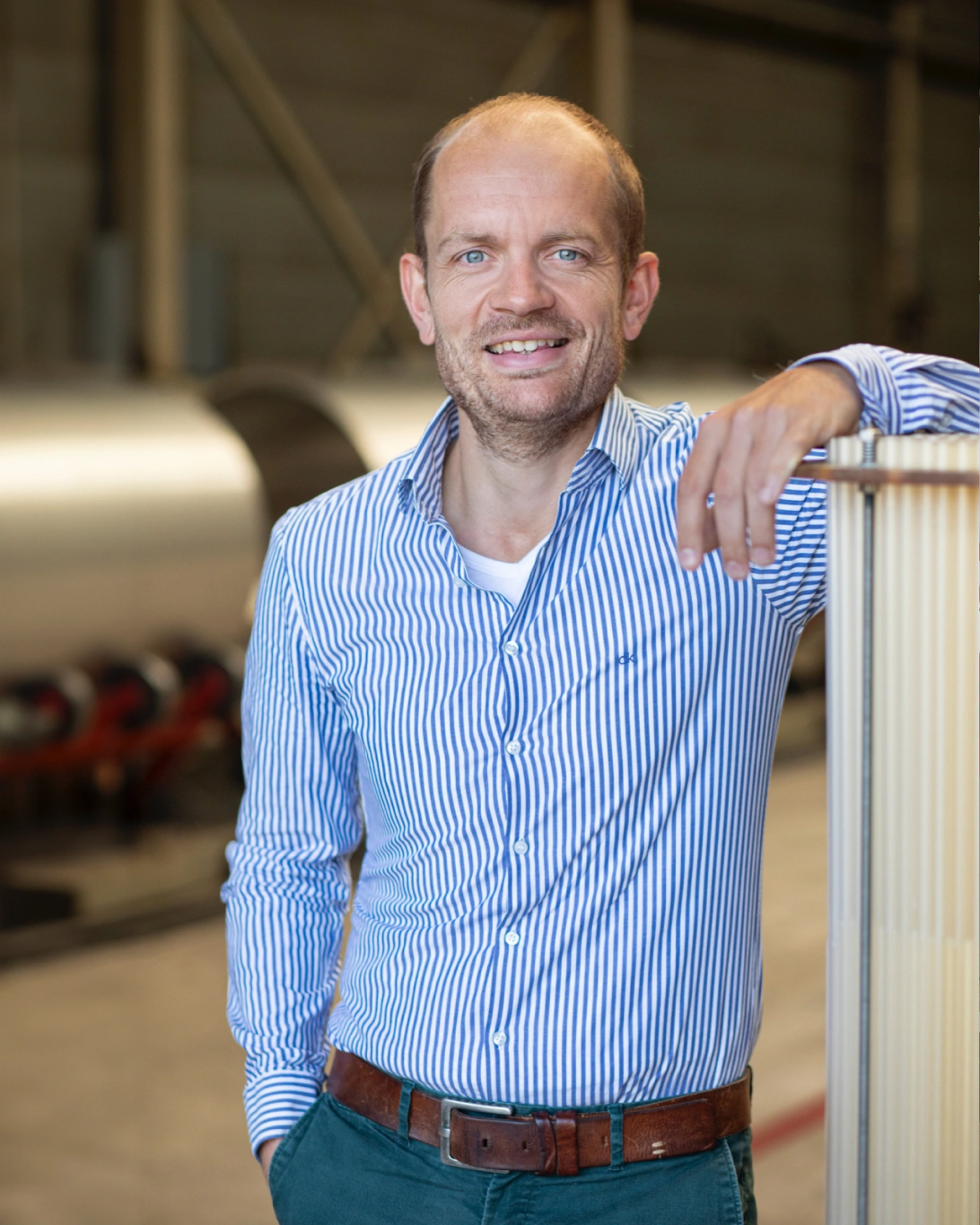
Contact
Curious about your savings potential?
A Heat Recovery Scan gives you quick insight into the most promising concepts for heat recovery, energy savings, reduction of CO2 emissions and payback period.