Food and beverage
Heat recovery for the food and beverage industry
In the food and beverage industry, heat recovery possibilities tend to be limited by corrosion and contamination. We put an end to that limitation with corrosion and dirt-resistant heat recovery systems that harness your residual heat for your primary or secondary processes.
So much potential!
15% of your energy is lost through flue gas or exhaust air leaving your chimney. Time for a change!
Significantly lower your annual energy costs
Structurally reduce your CO2 emissions
Prevent harmful corrosion and contamination
Breweries and distilleries
Breweries and distilleries have a strong focus on energy efficiency and water reduction. Heat can be recovered from the flue gas of the (bio)gas-fired boilers/CHPs and from the hot, wet exhaust streams of the process (wort boiling). Wort boiling accounts for 25-40% of total steam consumption. Heat Matrix managed to repurpose its residual heat in previous projects. We succeeded even with a biogas-fired steam boiler, where gases can be corrosive due to the sulphur content.
Dairy
The dairy industry uses boilers and dryers. A lot of heat is needed for drying, hot water cleaning and pasteurisation. A lot of the associated residual heat can be converted straight into the primary process. Even if fired with biogas and if the flue gases are corrosive.
Meat processors
Meat processors consume a lot of hot water from hot water boilers for cleaning purposes. In addition, flame furnaces are in use to burn hair and for disinfection purposes. Occasionally, biogas from the wastewater treatment plant is used as fuel. All these processes offer great opportunities for heat recovery from flue gas, with or without a heat pump.
Potato processing
In potato processing, peeling, blanching and frying are the main energy consumers. Energy savings and CO2reduction can be achieved through energy efficiency, material efficiency and fuel substitution. Heat Matrix supplies turnkey heat recovery systems for flue gas, drying air and fryer exhaust streams.
Sugar production
Refining sugar is an energy-intensive process. This means there is a lot to gain. We are happy to help you reduce the energy and water consumption of your boilers and dryers. Even if fired with biogas and if your flue gases are corrosive.
How heat recovery works
Capture residual heat …
When hot flue gas leaves your chimney, it still contains a significant amount of energy. Our heat recovery system captures this heat from steam or hot water boilers or CHP systems.
… And uses it to preheat air or water
The captured residual heat is used to heat combustion air, boiler feedwater, make-up water, cleaning water (CIP water) or central heating water. The result is an immediate drop in your fossil fuel consumption!
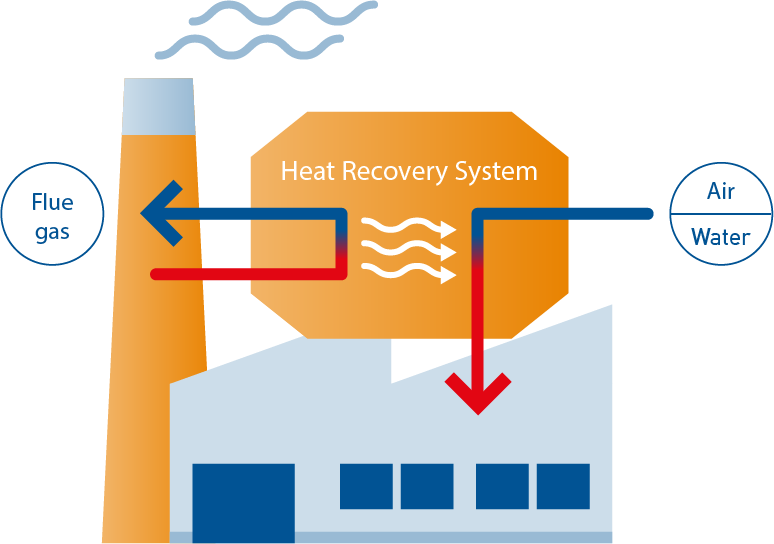
SOLUTIONS
Heat exchangers for the food and beverage industry
For residual heat recovery, we use heat exchangers that transfer residual heat to cold air streams (gas/gas heat exchangers) or heat exchangers that transfer residual heat to cold water or thermal oil (gas/liquid heat exchangers). The composition of the flue gas determines what material the heat exchanger is made of: metal or polymers. For corrosive or highly polluting flue gas, we opt for a polymer heat exchanger.
Our three clear promises
Gain insight into costs and benefits in advance
Corrosion and contamination-resistant systems
Payback periods of 3 to 5 years are feasible
Heat Matrix guarantees
- Expertise in industrial processes and heat integration.
- Substantial savings on energy costs and CO2 emissions.
- Maximum utilisation of residual heat.
- Insight into performance in advance and in hindsight.
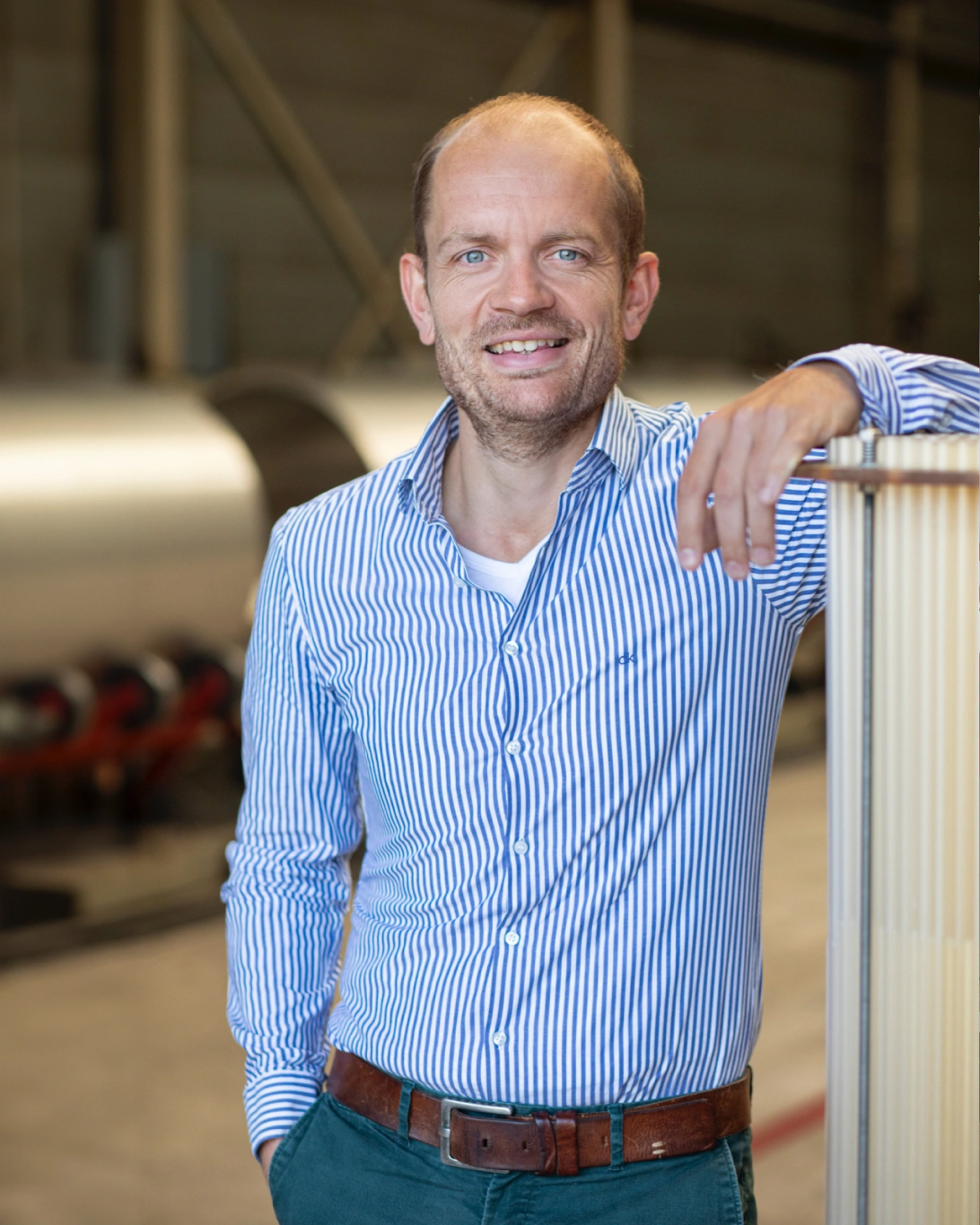
Contact
Curious about your savings potential?
A Heat Recovery Scan gives you quick insight into the most promising concepts for heat recovery, energy savings, reduction of CO2 emissions and payback period.