Manufacturing industry
Heat recovery in the manufacturing industry
A lot of heat, often at very high temperatures, is discarded in the manufacturing industry, broad as that term may be. Because the possibility of heat recovery was not thought of before, or because pollution problems and corrosion got in the way. Heat Matrix does away with these problems. With solutions that often pay for themselves within 3-5 years.
So much potential!
The sooner you deploy heat recovery, the faster you will start earning with this investment.
Significantly lower your annual energy costs
Structurally reduce your CO2 emissions
Prevent harmful corrosion and contamination
Bricks and roof tiles
Flue gas released from brick kilns contains acidic components such as HCl, HF and H2SO4. Dust and soot may be present as well. Our polymer technology allows us to recover heat from this flue gas despite corrosion and contamination. The preheated airflow can be used in the drying process, minimising gas consumption in the drying phase.
Paper and pulp
Several thermal processes occur in a paper and pulp mill: in steam boilers, CHP plants, dryers, RTOs and incinerators. A lot of heat is lost through the chimney, in the form of hot flue gas and as exhaust air from the dryer. This can amount to as much as 15% of primary energy consumption. This residual heat can be used to preheat the airflow to the incinerator or dryer, significantly reducing energy consumption and CO2 emissions. Alternatively, the residual heat can be used to heat boiler feed or process water.
Carpets
The carpet industry uses curing ovens. Their residual heat can be recovered and used to preheat the airflow to the oven. A second possibility is to use the residual heat to heat buildings. In this sector, 20-25% of annual gas consumption is used to heat buildings. Heat Matrix can design and build a complete plant that puts the residual heat to good use, significantly reducing energy consumption and CO2 emissions.
Galvanisation plants
The gas consumption of a galvanisation plant is typically 1 million standard cubic metres (Nm³) per year. Most of the gas is consumed by the zinc bath and the remainder for heating the treatment baths and heating buildings. Flue gases are released from the zinc furnace with a temperature exceeding 500⁰ C. We can use this heat for preheating the treatment baths, the drying phase and to heat buildings.
How heat recovery works
Capture residual heat …
When hot flue gases or exhaust air from your dryer leave the process, they still contain a significant amount of energy. Our heat recovery system captures this heat from your plant.
… And uses it to preheat air or water
The captured residual heat is used to preheat the air for your furnace or dryer. Your buildings can be heated with this residual heat as well. The result is an immediate drop in your fossil fuel consumption!
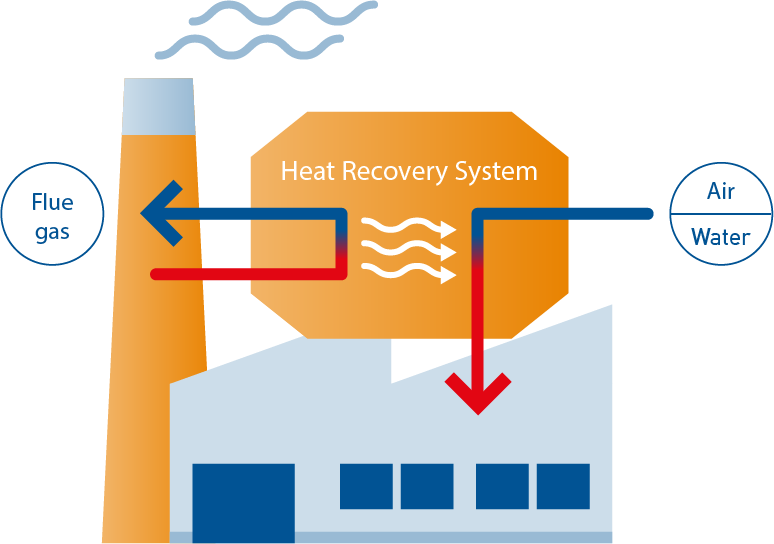
SOLUTIONS
Heat exchangers for the manufacturing industry
For residual heat recovery, we use heat exchangers that transfer residual heat to cold air streams (gas/gas heat exchangers) or heat exchangers that transfer residual heat to cold water or thermal oil (gas/liquid heat exchangers). The composition of the flue gas determines what material the heat exchanger is made of: metal or polymers. For corrosive or highly polluting flue gas, we opt for a polymer heat exchanger.
Our three clear promises
Gain insight into costs and benefits in advance
We deliver corrosion and contamination-resistant systems
Payback periods of 3 to 5 years are feasible
Heat Matrix guarantees
- Expertise in industrial processes and heat integration
- Substantial savings on CO2 emissions and energy costs
- Maximum utilisation of residual heat
- Insight into performance in advance and in hindsight
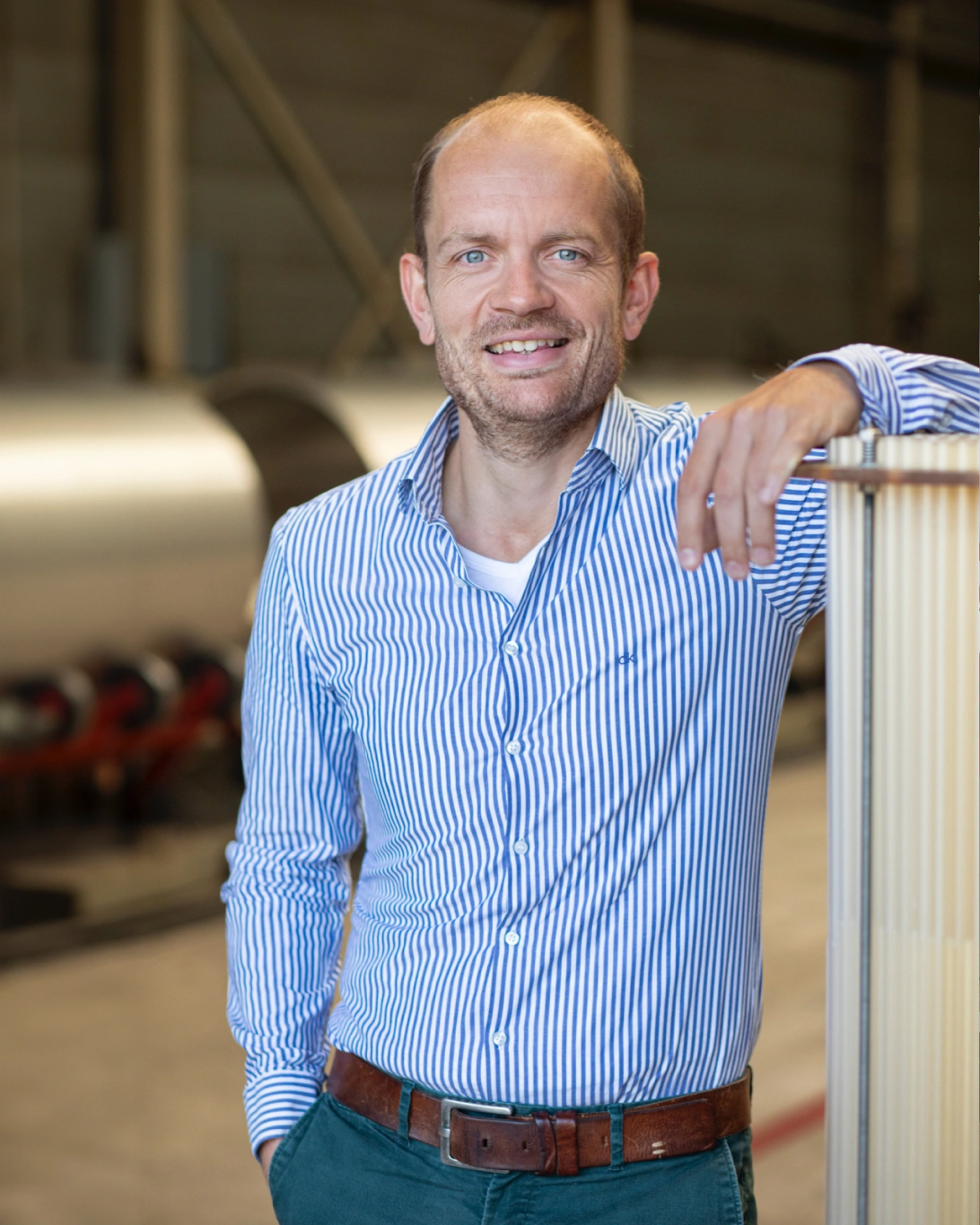
Contact
Curious about your savings potential?
A Heat Recovery Scan gives you quick insight into the most promising concepts for heat recovery, energy savings, reduction of CO2 emissions and payback period.