Corrosive
Heat recovery from corrosive or contaminating flue gases
Heat recovery from corrosive or contaminated flue gases is often challenging due to corrosion and fouling in heat exchangers. Heat Matrix offers innovative polymer heat exchangers that overcome these issues, enabling companies to save additional energy and reduce CO₂ emissions.
PROBLEM DEFINITION
Corrosion and fouling hinder heat recovery
Heat exchangers are needed to recover heat. But heat exchangers made of carbon steel or stainless steel suffer greatly in case of corrosive or highly contaminating flue gases. This is why Heat Matrix developed polymer heat exchangers that are corrosion-resistant and/or equipped with a built-in cleaning system. This allows companies with corrosive or highly contaminated flue gases to benefit from heat recovery.
Corrosive flue gases
Flue gases can contain corrosive elements when fuels containing, for example, sulphur (refinery gas, biogas, coal, oil and biomass) are used. Gases from drying or baking processes may also contain corrosive elements. The sulphur is converted into SO2 and SO3 during combustion, which can condense as sulphuric acid as the flue gas is cooled. The resulting sulphuric acid can then cause corrosion in heat exchangers when cooling below the acid dew point.
Contaminating flue gases
When exhaust gases or baking fumes containing contaminating elements are cooled too much, accumulation of dirt can occur. This can eventually lead to clogging of the heat exchanger.
SOLUTION
Polymer heat exchangers stop corrosion and fouling
The innovative heat exchangers with Polymer Honeycomb Technology (PHT) enable heat recovery from corrosive and contaminating flue gases. Of course, we also look at the corrosion resistance of the existing ductwork and adjust it, if necessary, when deploying these systems.
No corrosion
The PHT technology in polymer heat exchangers is resistant to acid formation. The polymers are resistant to H2SO4, HCl, HF and H3PO4, among others.
Reduced heat exchanger contamination
Contaminants have a difficult time sticking to the polymer walls in our heat exchangers. And for highly contaminating flue gases, we can install an internal cleaning system.
Extra heat recovery
Polymer heat exchangers even enable heat recovery below the acid dew point. The result: extra heat recovery!
METHOD
An efficient process and an optimal business case guaranteed
At Heat Matrix, we have extensive experience in understanding and analysing industrial processes. That is where we see opportunities that we can turn into heat recovery concepts based on our in-depth design expertise. And through our sister company Bos Nieuwerkerk, we have half a century of experience in execution. We are able to build any solution we come up with.
Our three clear promises
Gain insight into costs and benefits in advance
Corrosion and contamination-resistant systems
Payback periods of 3 to 5 years are feasible
Heat Matrix guarantees
- Expertise in industrial processes and heat integration
- Substantial savings on CO2 emissions and energy costs
- Maximum utilisation of residual heat
- Insight into performance in advance and in hindsight
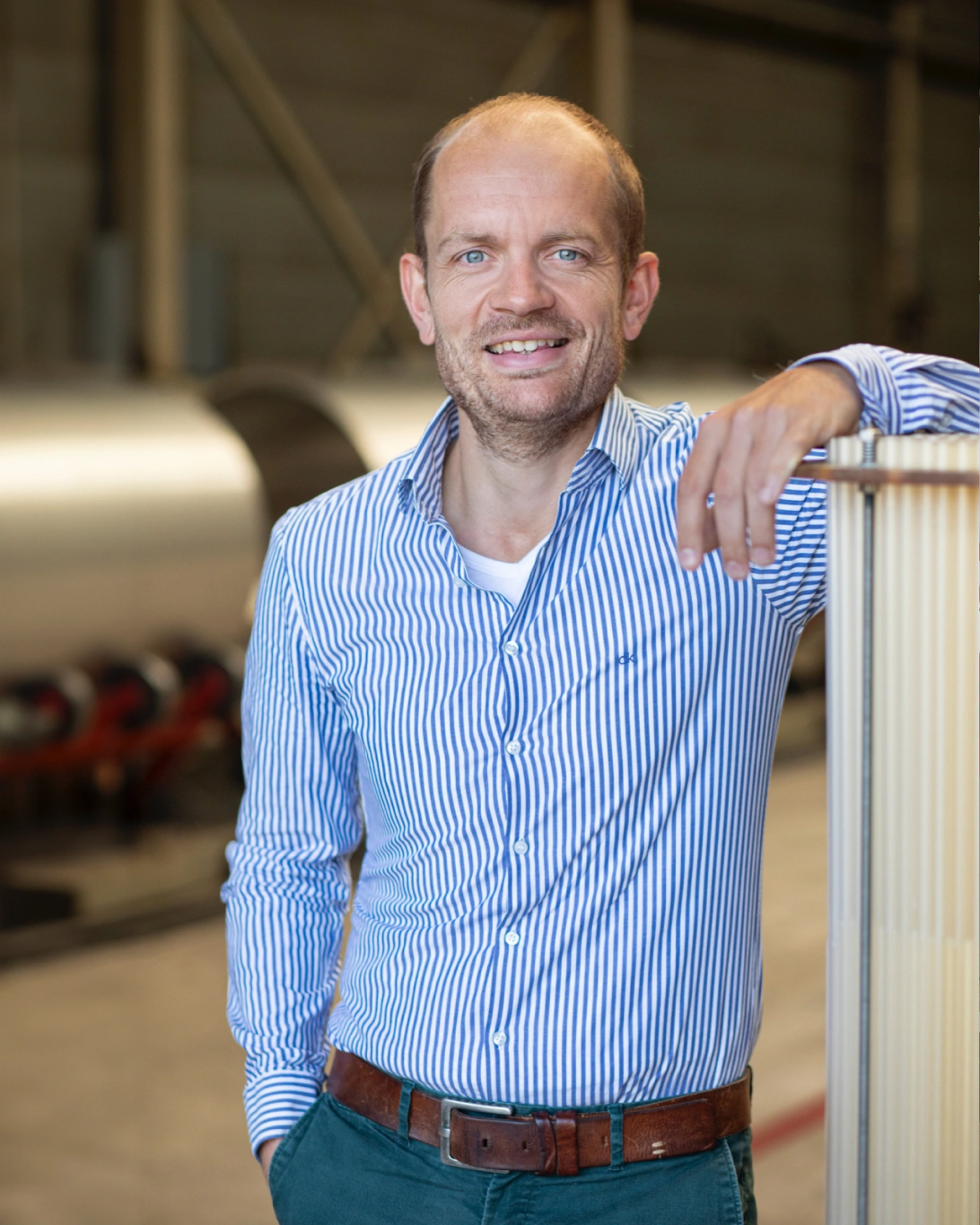
Contact
Curious about your savings potential?
A Heat Recovery Scan gives you quick insight into the most promising concepts for heat recovery, energy savings, reduction of CO2 emissions and payback period.