Reference
290 kW energy gain through heat integration at Sonac Loenen
At Sonac Loenen B.V., 81 °C flue gas from a dryer is used to preheat the supply air for that same dryer – from 10 to 52 °C. Thanks to polymer technology and an integrated cleaning system, this is done without any corrosion or fouling issues.
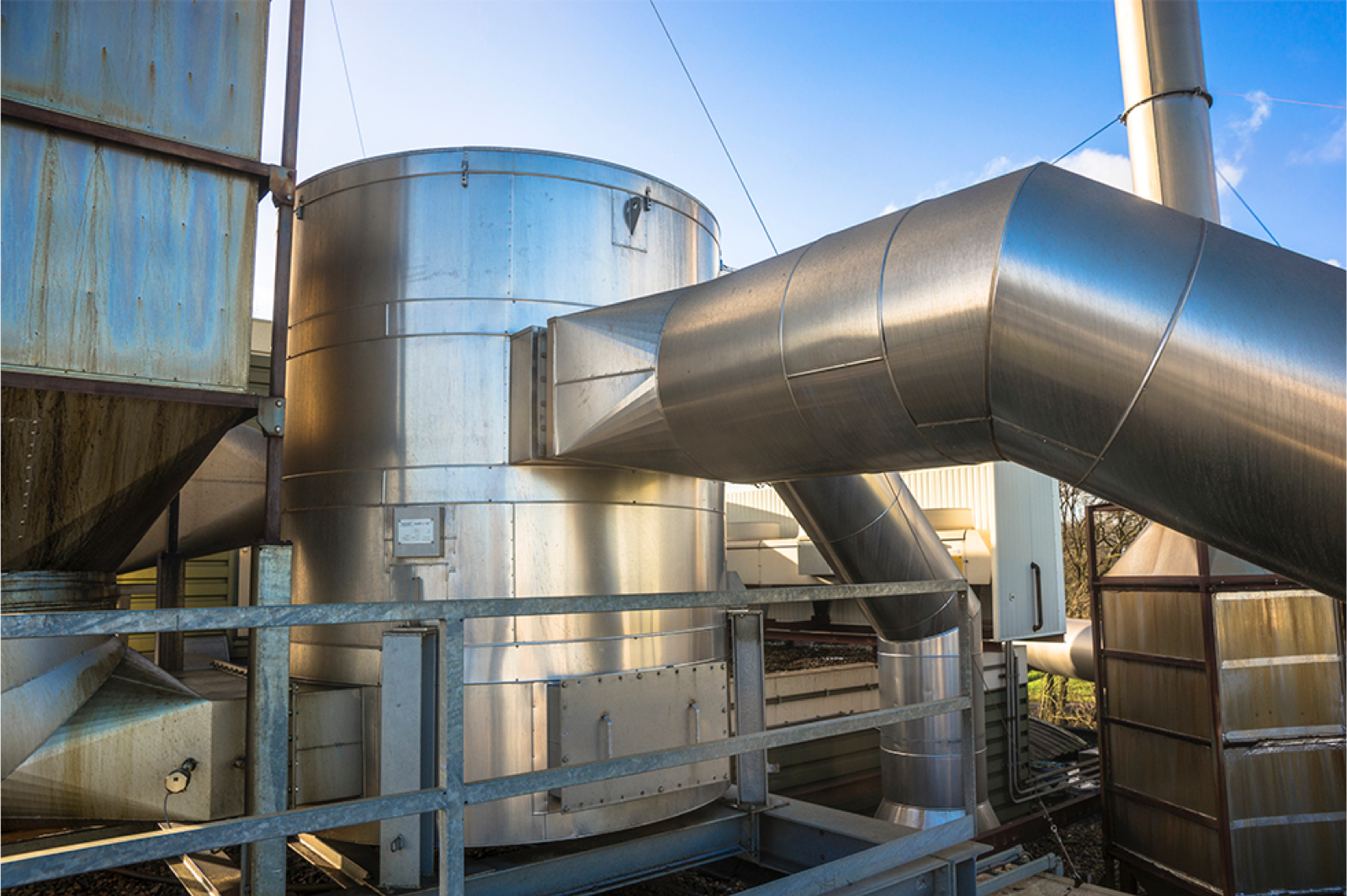
Polymer air preheater as a solution to corrosion and fouling
Sonac Loenen, a processor of animal blood into proteins, wanted to reduce the energy consumption of its production processes. A Heat Recovery Scan revealed that the dryer was a major consumer of natural gas. Heat recovery had previously been ruled out due to the fouling nature of the product and the corrosive cleaning agents used during CIP cycles.
Heat Matrix and sister company Bos Nieuwerkerk developed a solution using a polymer air preheater. This system extracts heat from the 81 °C flue gas to preheat the incoming air for the dryer from 10 to 52 °C.
Efficient installation and long-term performance without problems
The heat recovery concept was designed together with Bos Nieuwerkerk, who then engineered, produced and installed the system in-house. Heat Matrix handled commissioning. The system has now been running for over five years, recovering 290 kW of thermal energy.
Specifications
- Operating hours6,000 hrs/year
- Flue gas flow27,000 kg/hr
- Flue gas temperature81 °C
- Air flow24,600 kg/hr
- Air temperature10 °C
- Heat exchangerPolymer air preheater
- Recovered power290 kW
- Energy savings6,264 GJ/year
- CO₂ reduction352 tons/year
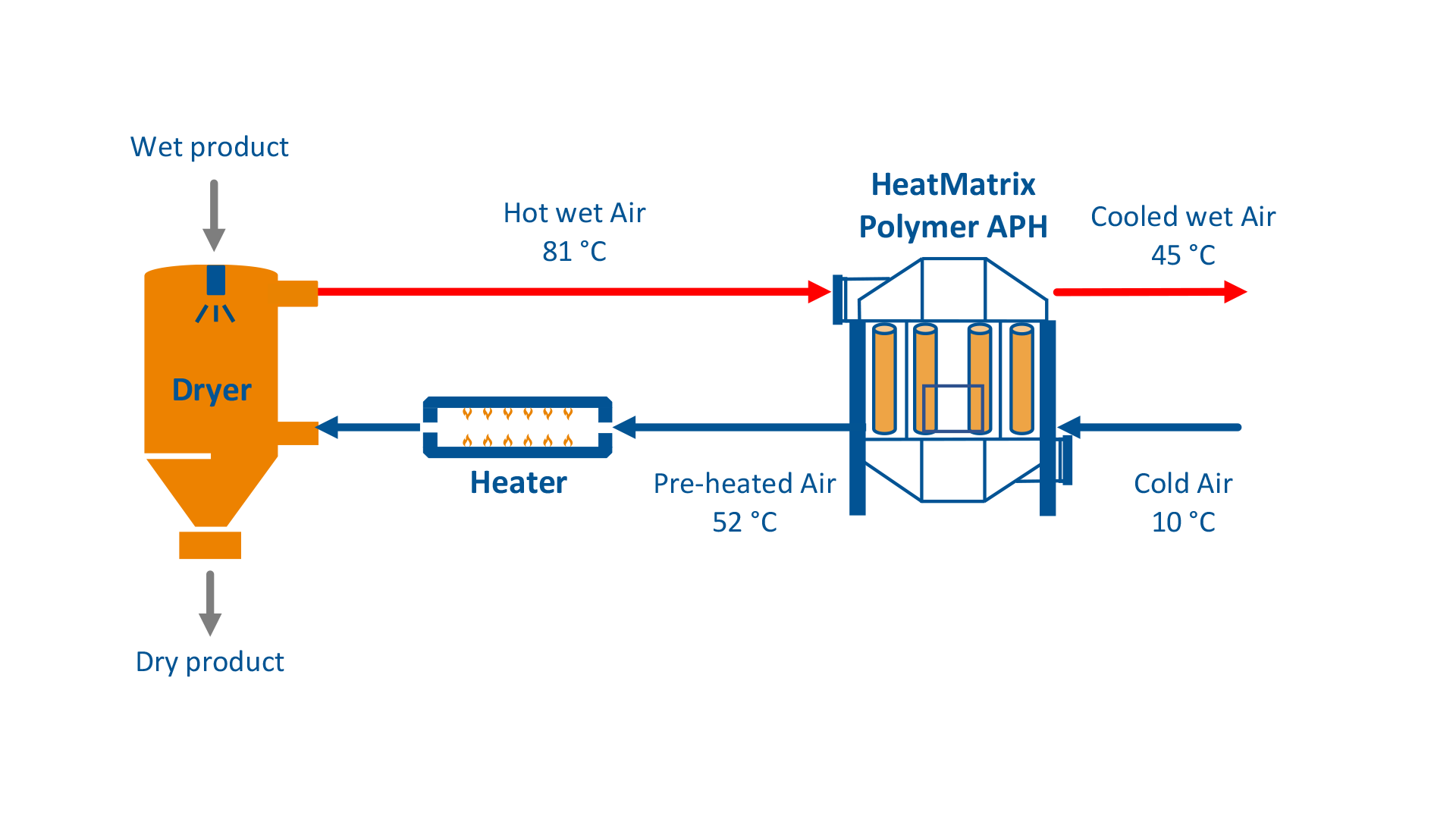
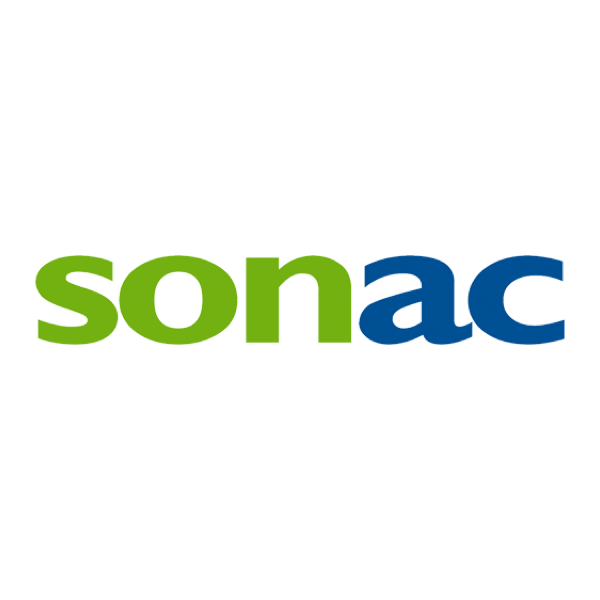
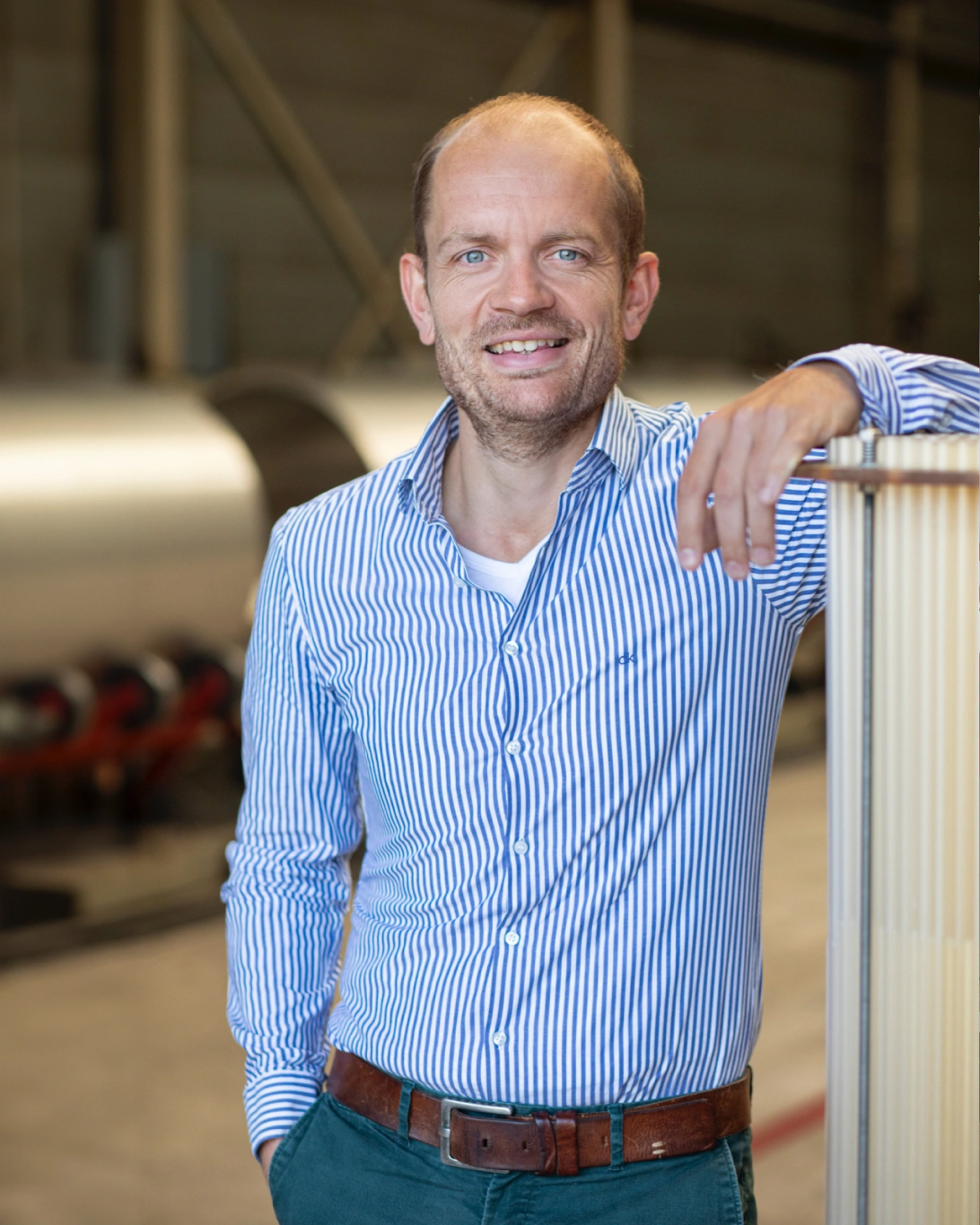
Contact
Curious about your savings potential?
A Heat Recovery Scan gives you quick insight into the most promising concepts for heat recovery, energy savings, reduction of CO2 emissions and payback period.
Related references