Reference
Aviko Rixona saves 220 tons of CO₂ annually
To reduce CO₂ emissions, Aviko Rixona teamed up with Heat Matrix to recover heat from the 170 °C flue gases of their steam boiler. A polymer air preheater prevented corrosion from the biogas. The result: 130 kW energy savings and a 220-ton reduction in CO₂ emissions per year.
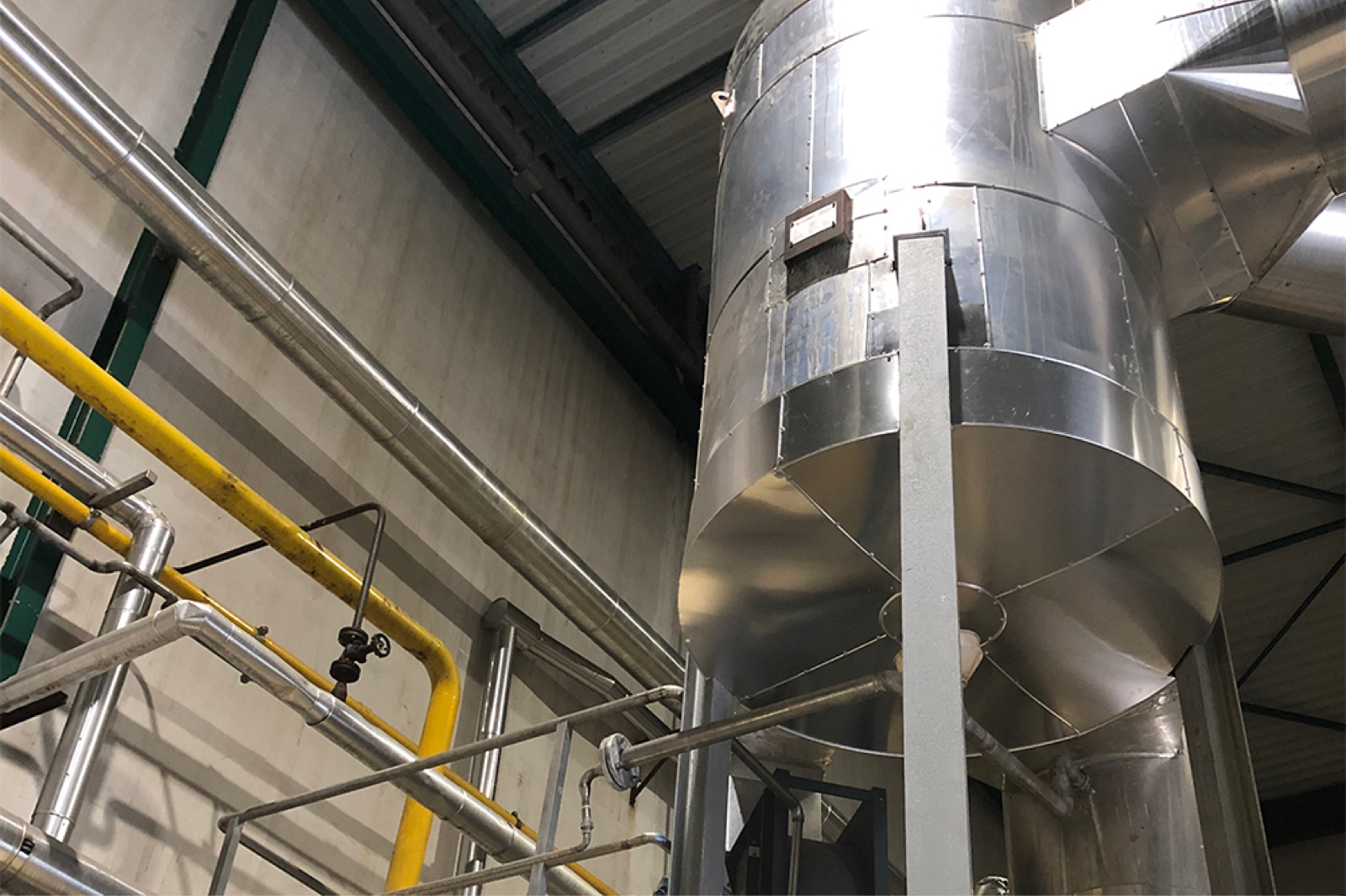
Heat recovery from biogas flue gases
Aviko Rixona aimed to lower its CO₂ emissions. Heat Matrix identified an opportunity for heat recovery from the 170 °C flue gases of the steam boiler. The boiler is partly fueled by biogas, which contains sulphur. Because of this, heat recovery from the flue gases had previously been ruled out due to the high risk of corrosion in the heat exchanger.
Polymer air preheater
We proposed a polymer air preheater that made heat recovery from corrosive flue gases possible. The hot flue gases from the biogas-fired boiler are now used to preheat incoming air from 15 to 118 °C. The recovered energy yields a saving of 130 kW and reduces CO₂ emissions by 220 tons per year. No corrosion issues have been observed in either the heat exchanger or the chimney.
Specifications
- Operating hours7,200 h/year
- Boiler capacity5.5 MW
- Flue gas flow4,600 kg/h
- • Flue gas temperature170 °C
- Heat exchangerPolymer air preheater
- Energy saved130 kW
- Annual energy savings3,369.6 GJ
- Annual CO₂ reduction190 tons
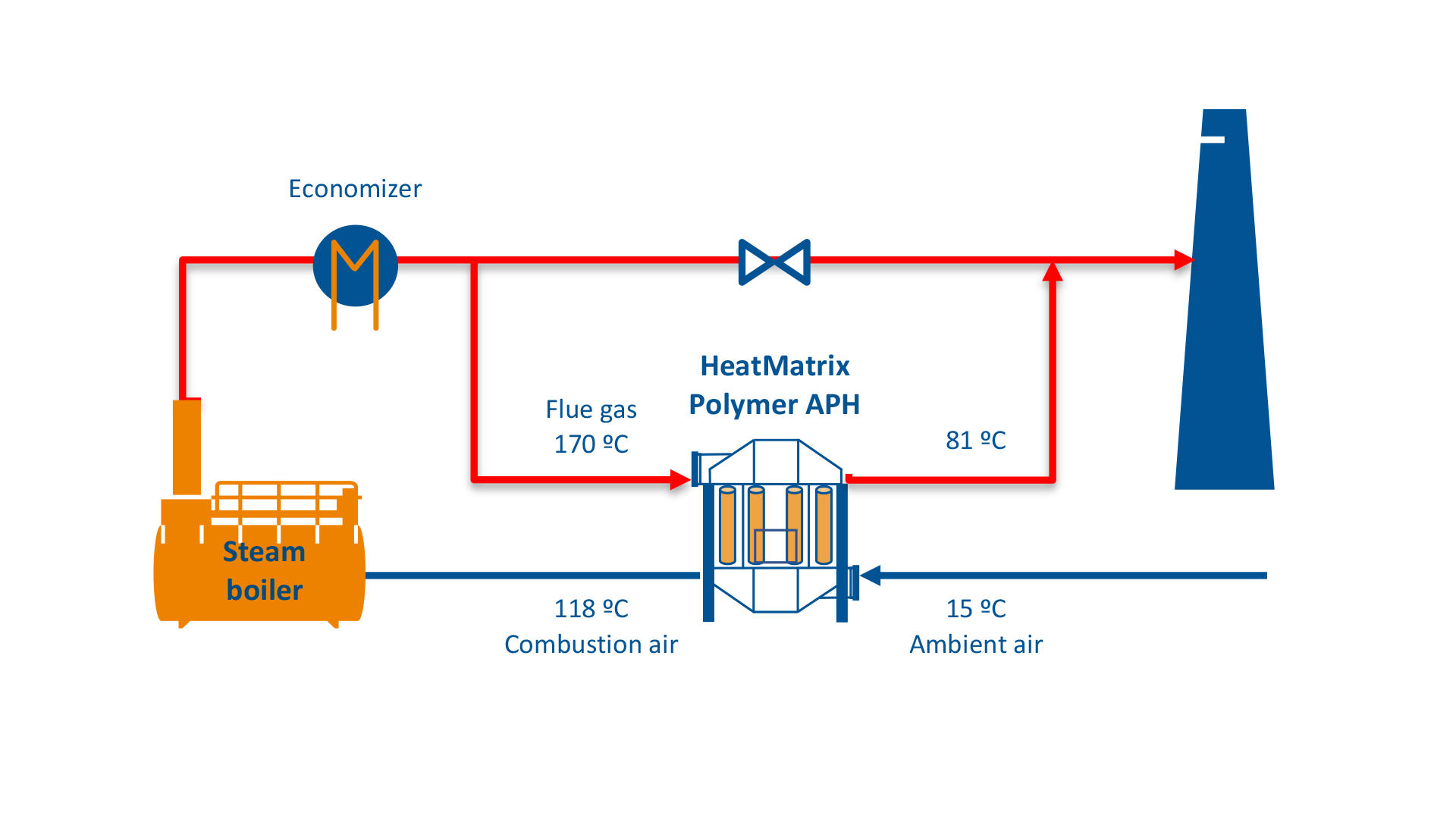
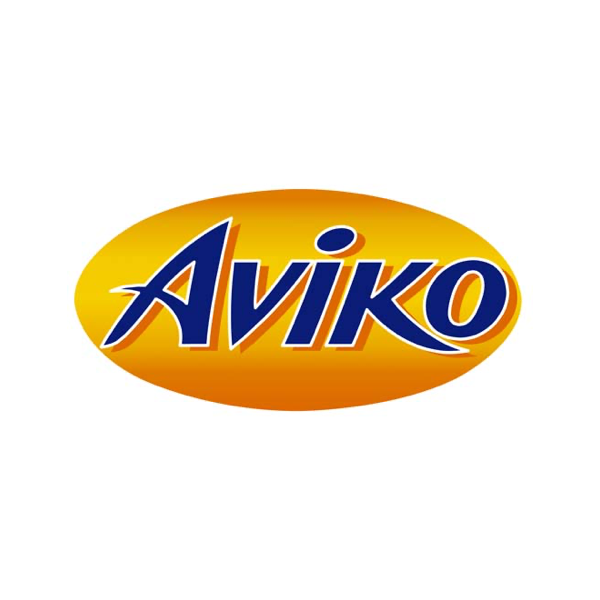
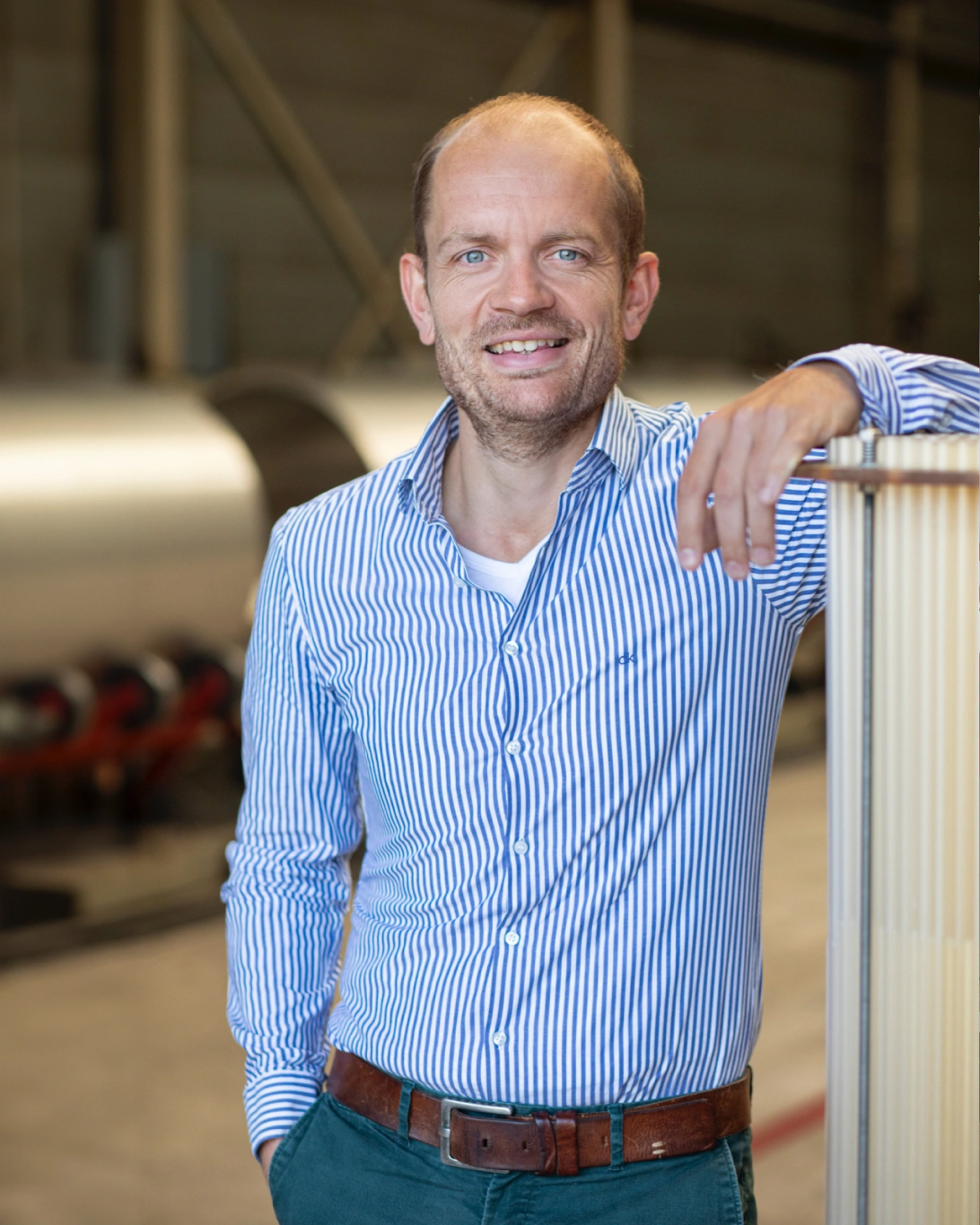
Contact
Curious about your savings potential?
A Heat Recovery Scan gives you quick insight into the most promising concepts for heat recovery, energy savings, reduction of CO2 emissions and payback period.
Related references