Reference
4% higher boiler efficiency for Carlsberg
For global brewer Carlsberg, we implemented a heat recovery system that captures energy from corrosive flue gases from a biogas-fired steam boiler. The combustion air is preheated to 80°C, resulting in a system output of 290 kW and a 4% increase in boiler efficiency.
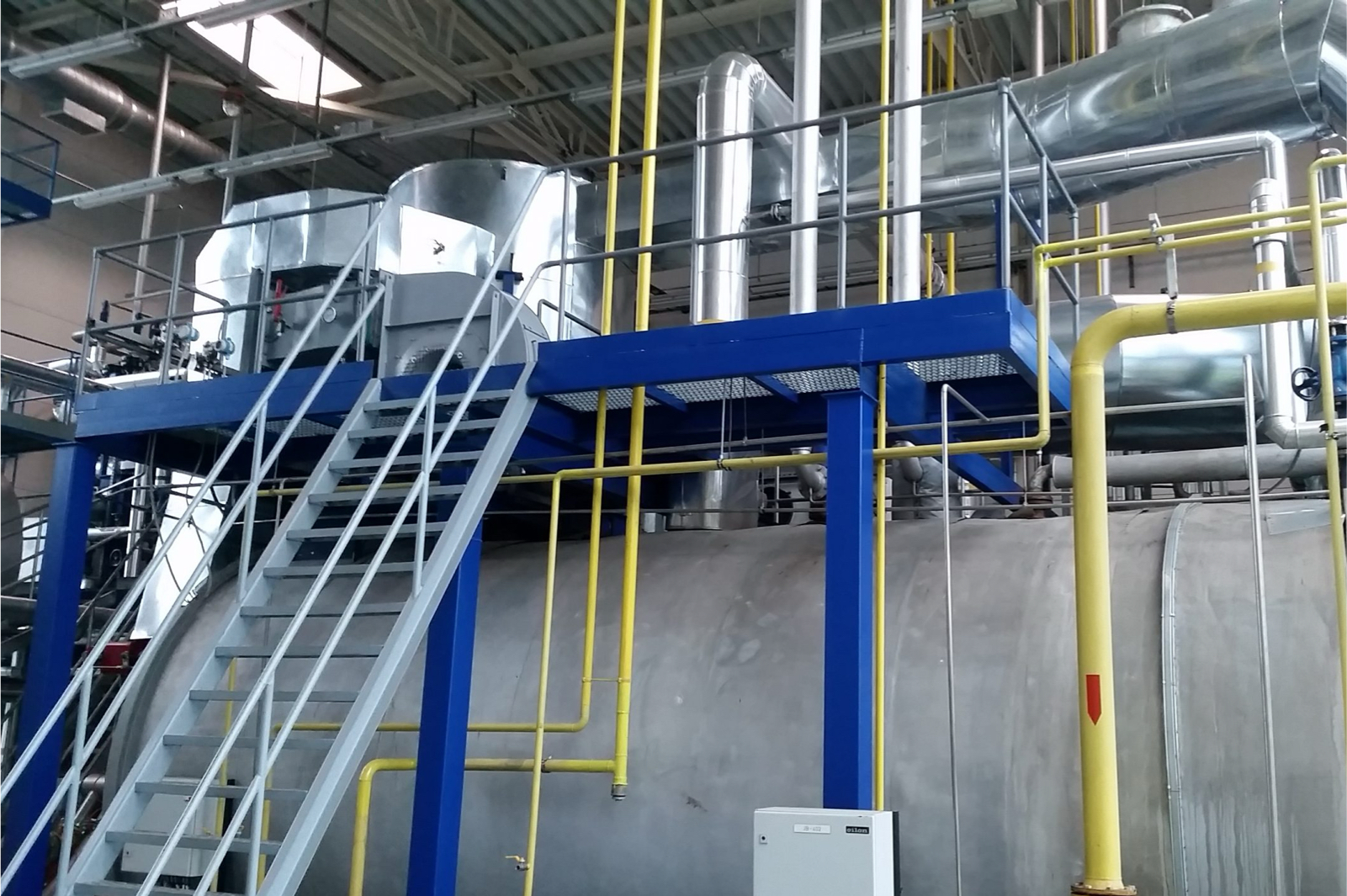
Sustainable innovation at Carlsberg
As part of its Together Towards ZERO programme, Carlsberg is committed to making its breweries more sustainable. One such step was the switch to a biogas-fired steam boiler. However, this choice led to high sulphur concentrations in the flue gas. When cooled, this gas forms sulphuric acid, which is highly corrosive and made heat recovery previously unfeasible. The 140°C+ flue gases were simply vented through the chimney.
Corrosion-resistant air preheater
Heat Matrix and Bos Nieuwerkerk designed, built, and installed a polymer air preheater resistant to acid corrosion. This made heat recovery below the acid dew point possible. The heat exchanger delivers 290 kW and preheats the boiler combustion air to 80°C, improving boiler efficiency by 4%.
Specifications
- Boiler capacity20 THP
- Operating hours8,000 h/year
- Flue gas flow15.000 kg/h
- Flue gas temperature142 °C
- SO₂ concentration71,5 mg/Nm³
- Heat exchangerPolymer air preheater
- Recovered output290 kW
- Recovered energy8.352 GJ/year
- CO₂ reduction470 tons/year
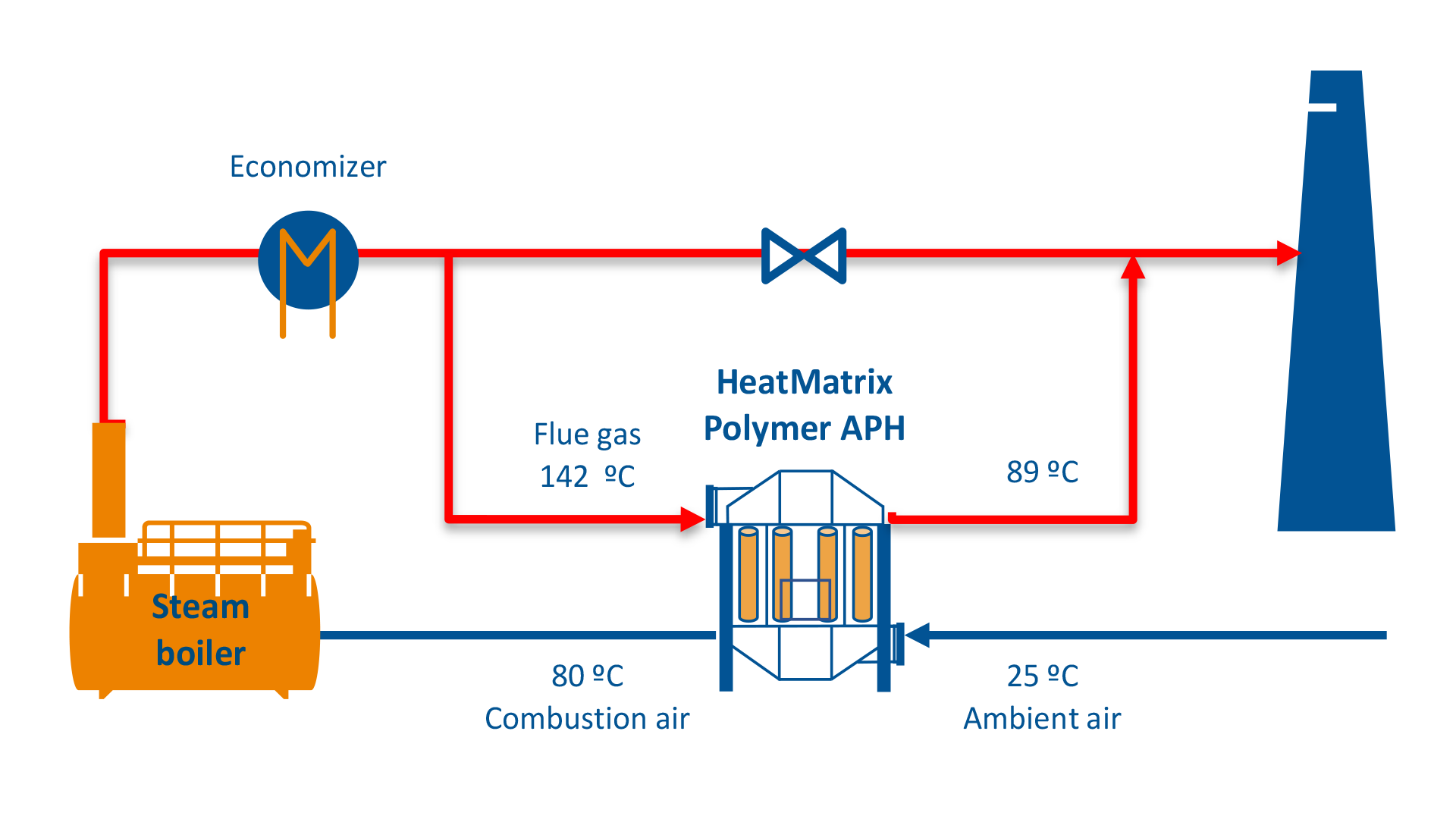
“The polymer air preheater from Heat Matrix enabled us to recover additional residual heat from our steam boiler. Efficiency increased by 4%, with no corrosion issues.”
Dmytro Markovsky, Plant manager Carlsberg
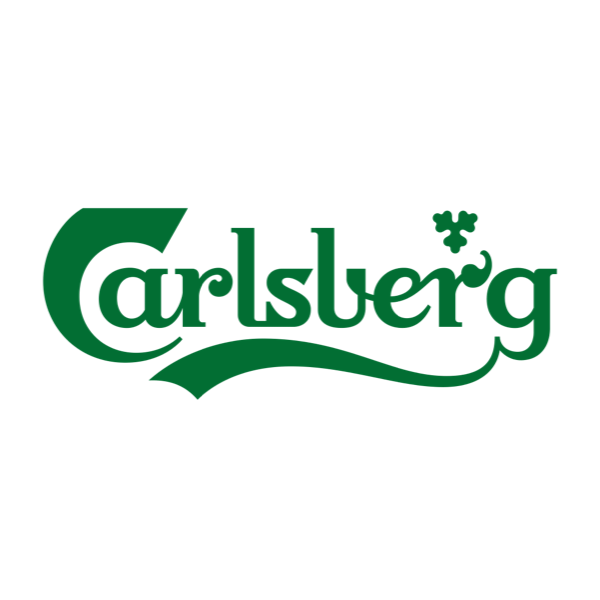
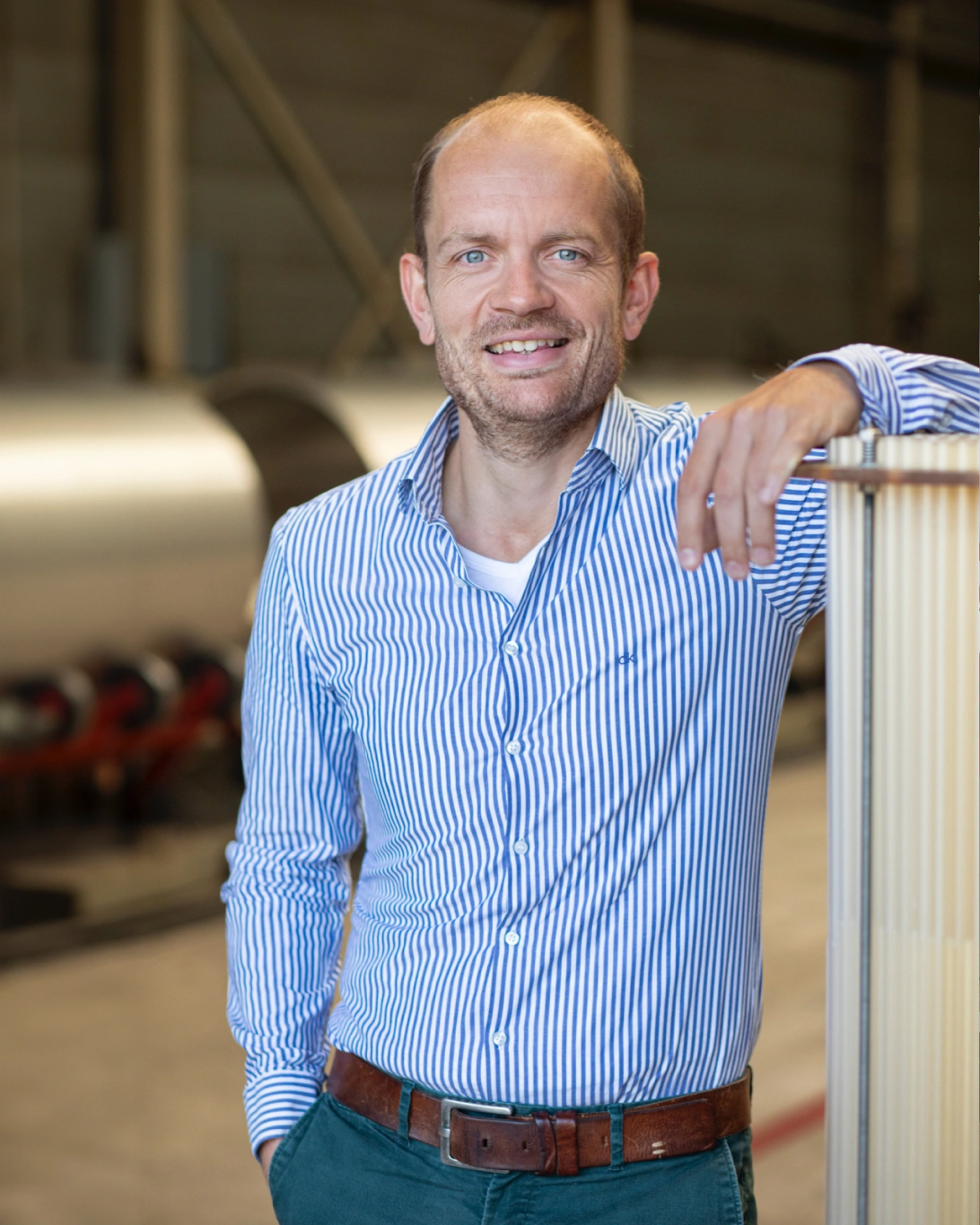
Contact
Curious about your savings potential?
A Heat Recovery Scan gives you quick insight into the most promising concepts for heat recovery, energy savings, reduction of CO2 emissions and payback period.
Related references