Reference
Heat recovery for biogas-fired water treatment plant
For a water treatment facility, Heat Matrix developed a system to recover heat from biogas flue gases. The system is expected to deliver 191 kW of thermal output, heating 8,000 litres of water per hour from 75 to 90 °C.
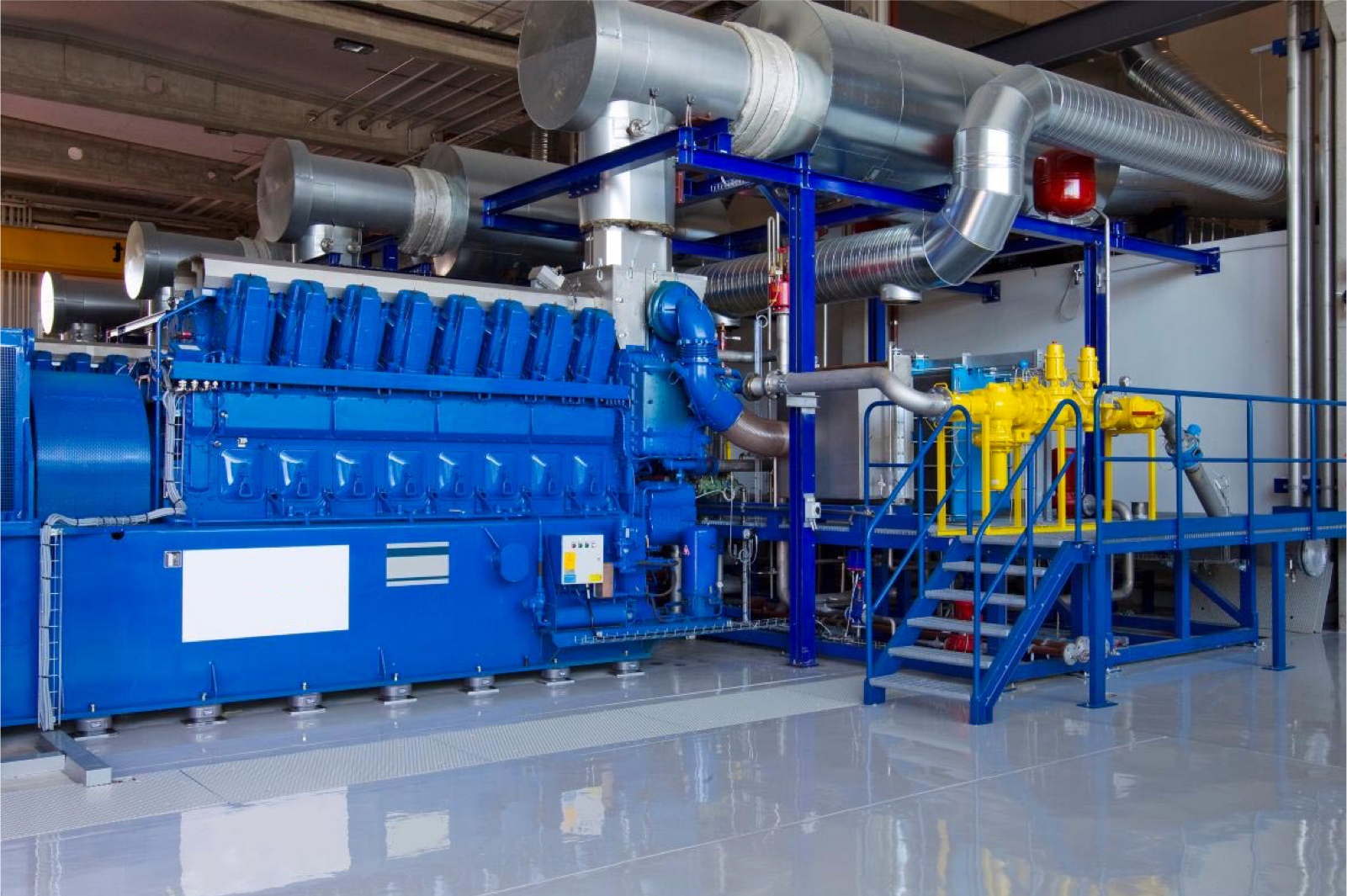
Sustainable energy solution for wastewater treatment
A wastewater treatment facility aimed to generate electricity and heat using a CHP unit fired with biogas from its anaerobic treatment process. To maximise sustainability and efficiency, the facility wanted to recover heat from the flue gas. However, biogas contains hydrogen sulfide (H₂S), which makes the flue gases corrosive when cooled—posing a serious challenge for conventional heat exchangers.
Proprietary corrosion-resistant heat exchanger
Heat Matrix designed a heat recovery system using its proprietary corrosion-resistant polymer heat exchanger. The corrosive flue gases from the four biogas engines of the CHP system are routed through a central duct into this polymer economiser. The flue gas is cooled below the acid dew point, allowing additional heat to be recovered safely.
191 kW heat recovery
Cooling the flue gas from 180 to 102 °C results in a thermal gain of 191 kW. This energy is used to heat 8,000 kg of water per hour from 75 to 90 °C—without any corrosion issues.
Specifications
- Operating hours8,400 h/year
- Flue gas flow8,000 kg/h
- Flue gas temperature180 °C
- SO₂ concentration800 mg/Nm³
- Heat exchangerPolymer economiser
- Energy saved191 kW
- Annual energy savings5,775.84 GJ
- Annual CO₂ reduction325 tons
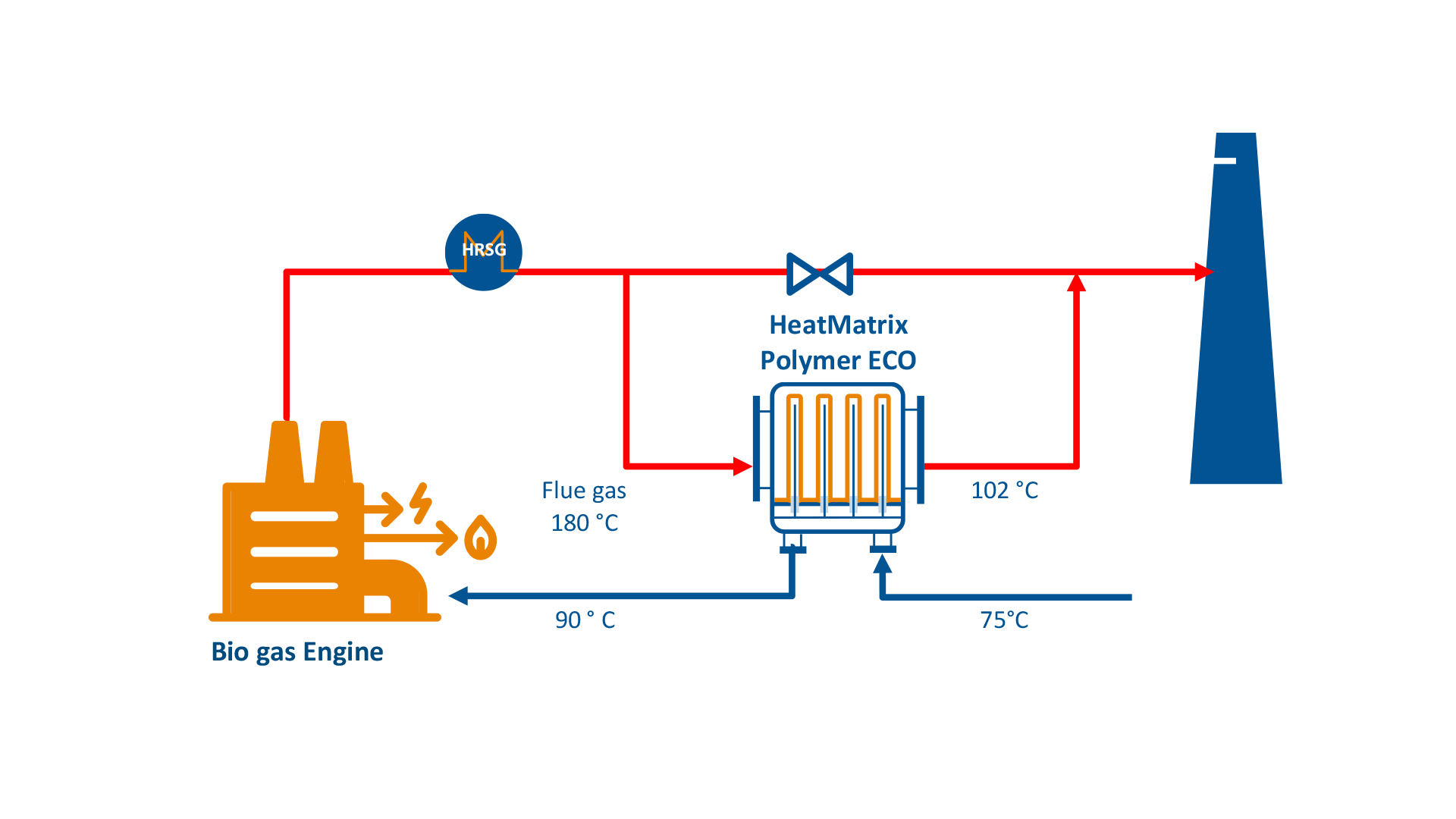
“Heat Matrix helped us explore our sustainability options. Their technical assessment made the polymer economiser a serious contender for our future energy plans.”
— Operations Manager, Water Treatment Facility
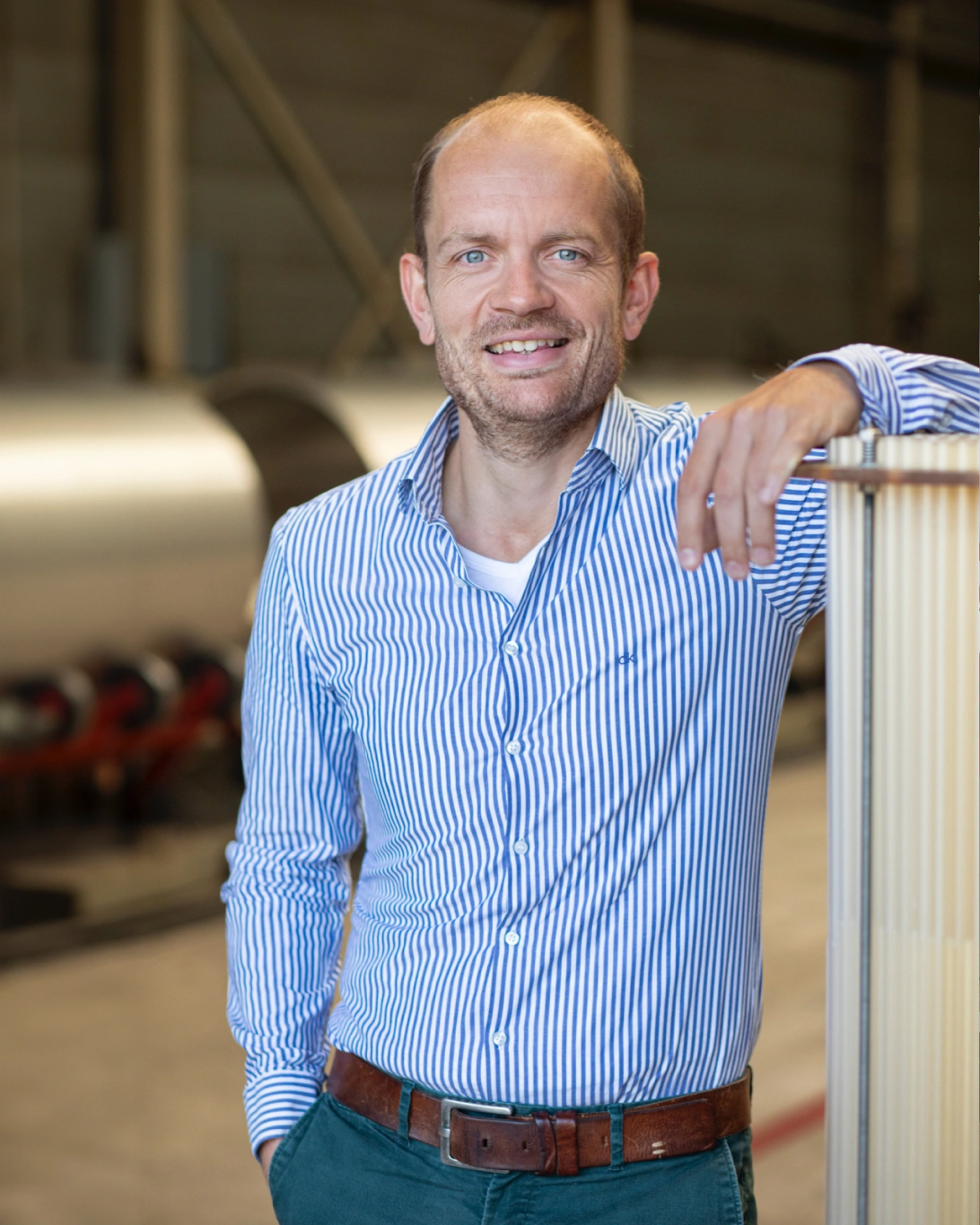
Contact
Curious about your savings potential?
A Heat Recovery Scan gives you quick insight into the most promising concepts for heat recovery, energy savings, reduction of CO2 emissions and payback period.
Related references