Reference
Heat recovery from baking fumes: 140 kW at biscuit factory
An industrial biscuit manufacturer reduced oven gas consumption by 20% through heat recovery from baking fumes. A polymer air preheater with self-cleaning system prevents fouling and ensures more stable production with shorter baking times.
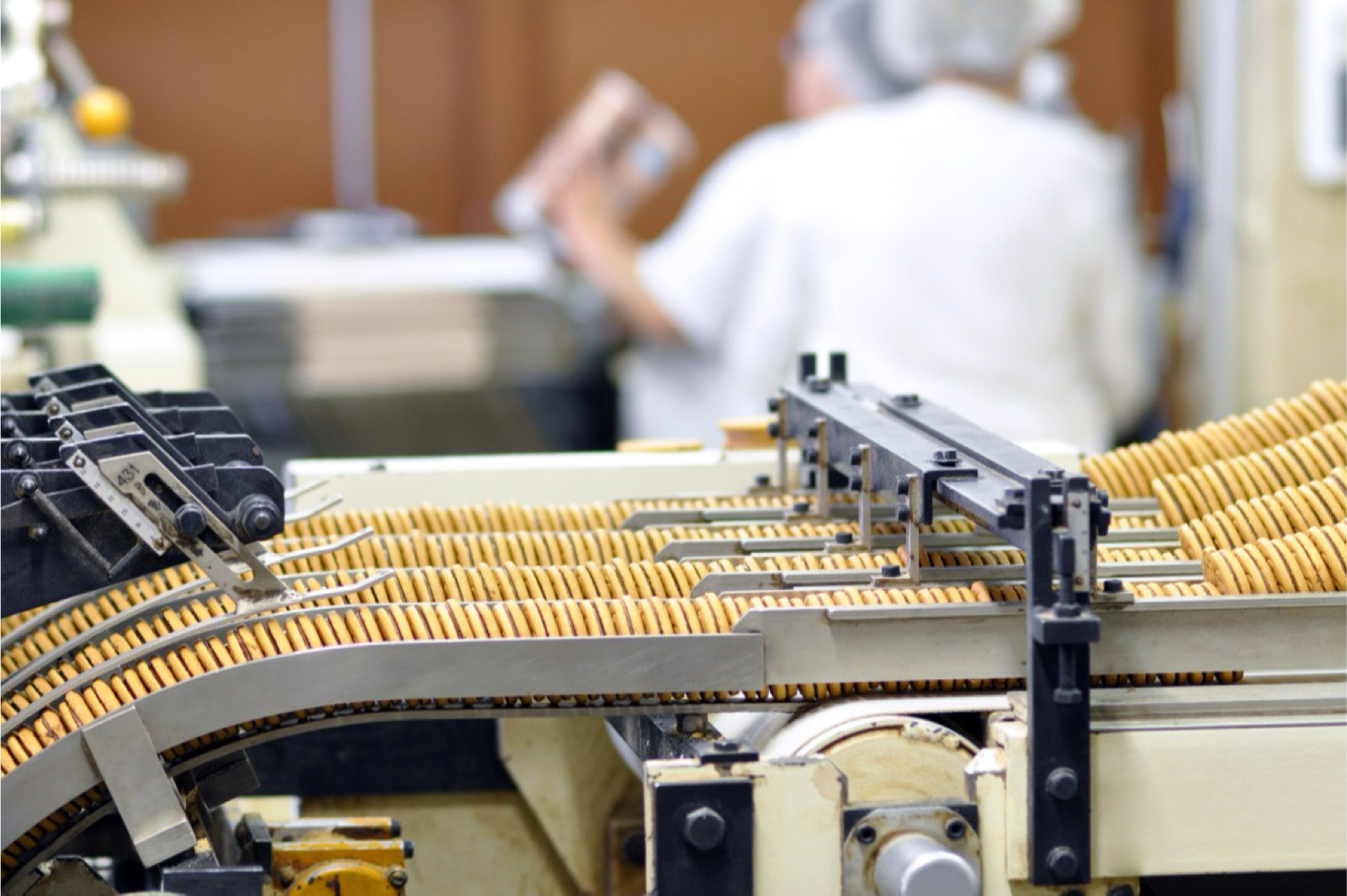
Saving energy with heat recovery from baking fumes
The biscuit manufacturer was looking for ways to reduce energy use by recovering heat from flue gases. During our Heat Recovery Scan, the oven was identified as the most promising source of residual heat. Hot, polluted baking fumes at 165 °C were escaping through the chimney.
Self-cleaning heat exchanger for contaminated flue gases
A polymer air preheater proved to be the optimal solution for this bakery. The polymer material reduces the adhesion of contaminating particles, while the built-in internal cleaning system efficiently removes any remaining fouling. Our sister company Bos Nieuwerkerk took care of engineering, production and installation of the entire system.
20% gas savings
Thanks to the heat recovery system, oven recirculation air is preheated from 15 °C to 103 °C. This results in 140 kW of recovered heat and a 20% reduction in the oven’s gas consumption.
Specifications
- Operating hours6.000 u/jaar
- Flue gas flow6,100 kg/uur
- Flue gas temperature165 °C
- Heat exchangerPolymere luchtvoorverwarmer
- Recovered power140 kW
- Energy saved3024 GJ/jaar
- Oven gas reduction20%
- CO₂ reduction170 ton/jaar
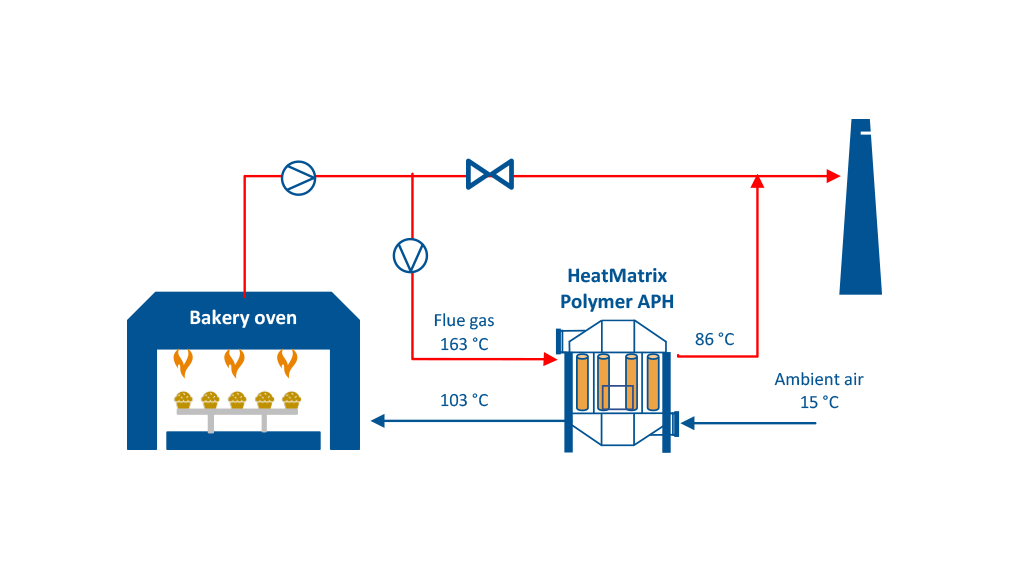
“Installing the polymer air preheater reduced our gas consumption by 20%. It also improved temperature uniformity in the oven, resulting in more stable production and shorter baking times.”
— Head of Technical Services
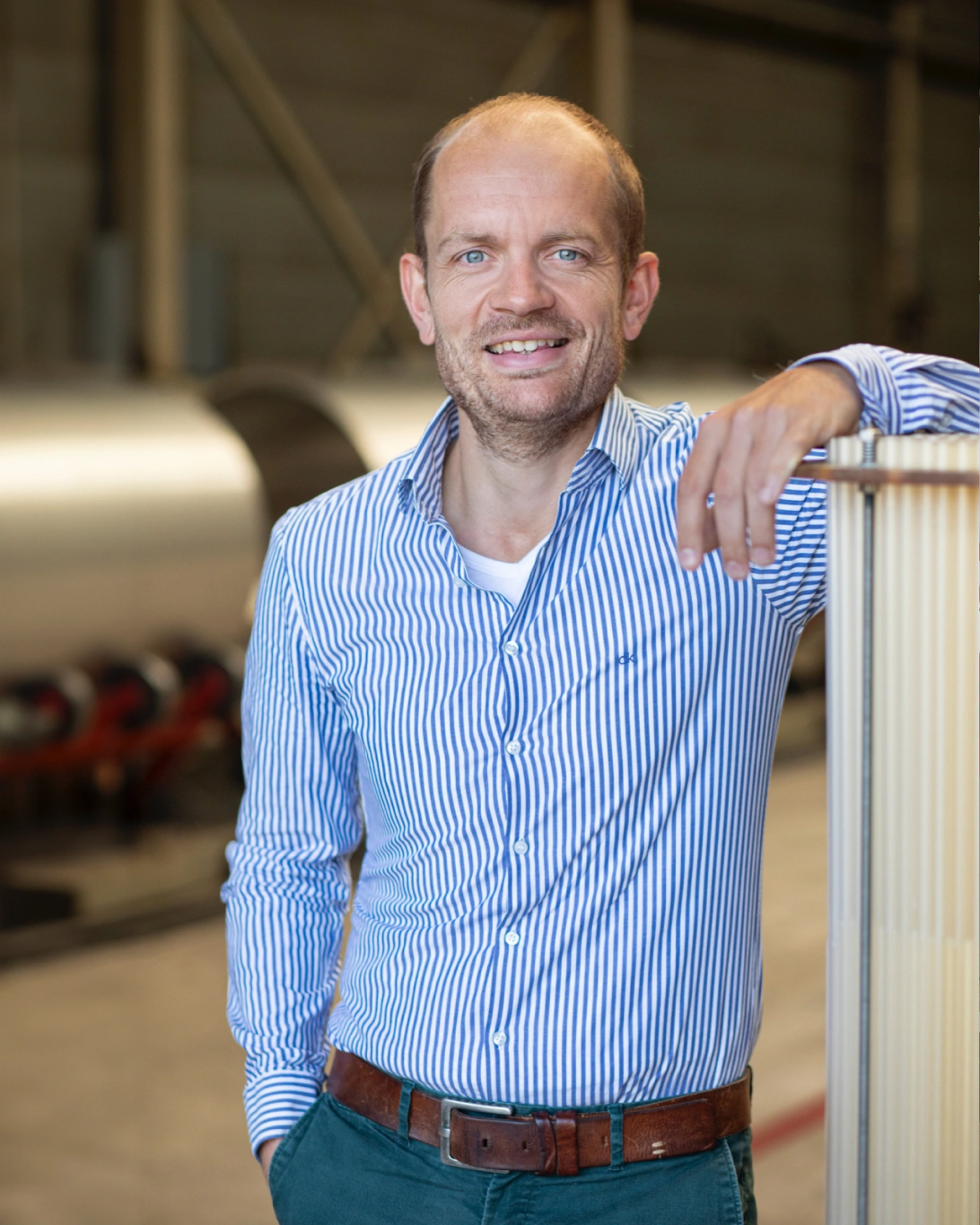
Contact
Curious about your savings potential?
A Heat Recovery Scan gives you quick insight into the most promising concepts for heat recovery, energy savings, reduction of CO2 emissions and payback period.
Related references