Reference
Heat recovery from corrosive flue gases at refinery
A refinery was losing large amounts of energy through corrosive flue gases. To reduce CO₂ emissions, Heat Matrix installed a sulphuric acid-resistant air preheater. With a capacity of 3,200 kW, this system improved the furnace efficiency by 4%.
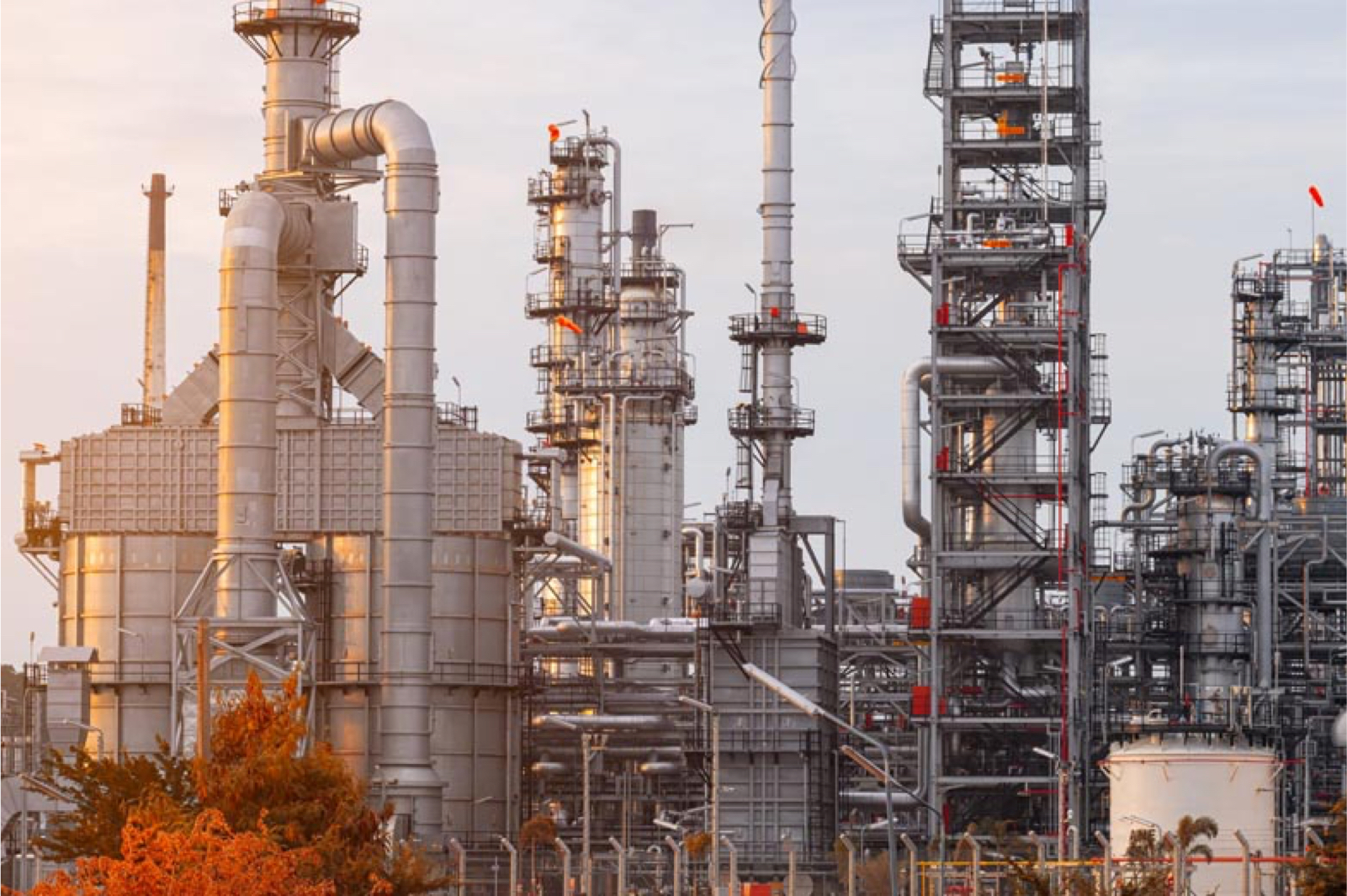
Unlocking heat recovery from corrosive flue gas
A refinery was losing substantial energy through corrosive flue gases, which had previously ruled out heat recovery. Cooling these flue gases leads to the formation of sulphuric acid, which can severely damage a conventional heat exchanger.
Air preheater with 3,200 kW capacity
Heat Matrix solved this challenge by designing a polymer air preheater. Polymer is resistant to sulphuric acid, making heat recovery feasible under these conditions. Following production and installation, the preheater—delivering 3,200 kW—boosted furnace efficiency by 4%. The downstream corrosion rate remains below 0.1 millimetres per year.
Specifications
- Operating hours8,400 h/year
- Flue gas flow123,000 kg/h
- Flue gas temperature180 °C
- SO₂ concentrationUp to 100 mg/Nm³
- Heat exchangerPolymer air preheater
- Energy saved3.200 kW
- Annual energy savings96,768 GJ
- Annual CO₂ reduction5,442 tons
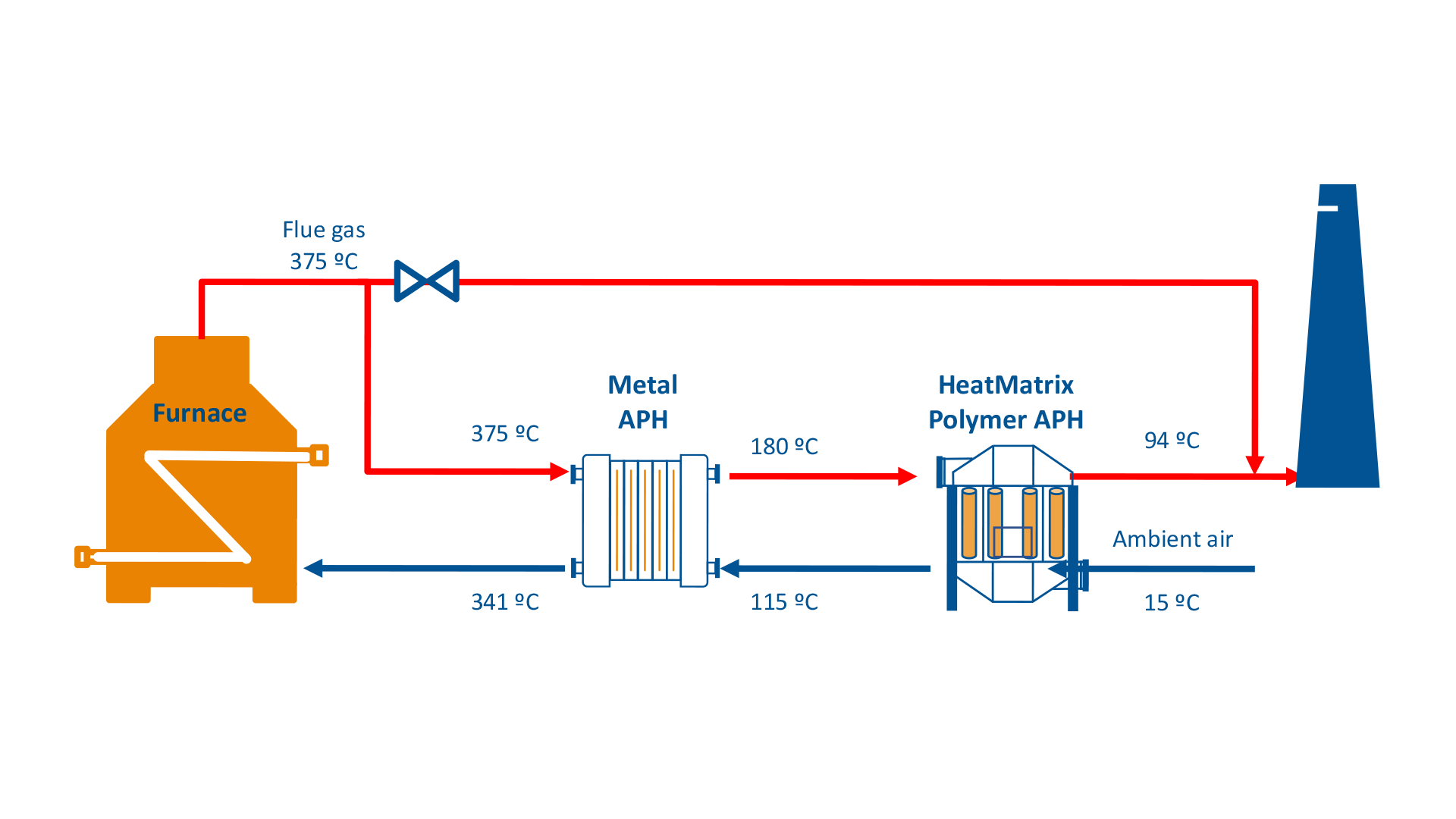
“We are strongly committed to reducing our CO₂ emissions. Improving furnace efficiency plays a key role in that effort. Heat Matrix made heat recovery in our refinery possible.”
— Head of Production Optimization
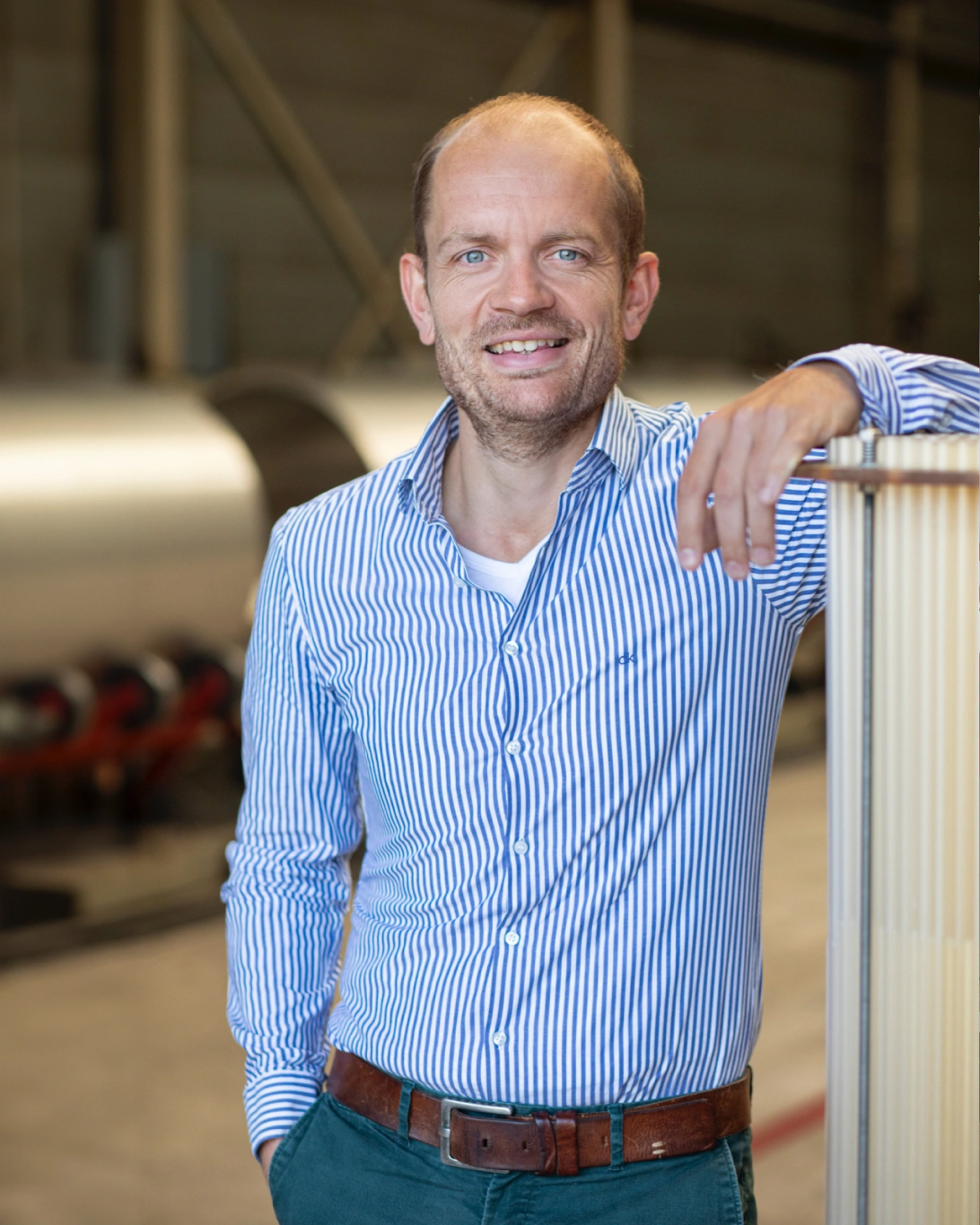
Contact
Curious about your savings potential?
A Heat Recovery Scan gives you quick insight into the most promising concepts for heat recovery, energy savings, reduction of CO2 emissions and payback period.
Related references