Reference
8% lower energy consumption through heat recovery at Lubrizol
At its CPVC (thermoplastic) production site in Farmsum (Groningen), Lubrizol was looking for ways to reduce the energy use of its drying processes. We recovered heat from corrosive flue gases to preheat the incoming air for the dryer from 10 to 56 °C. This resulted in an energy saving of 170 kW – without any corrosion issues.
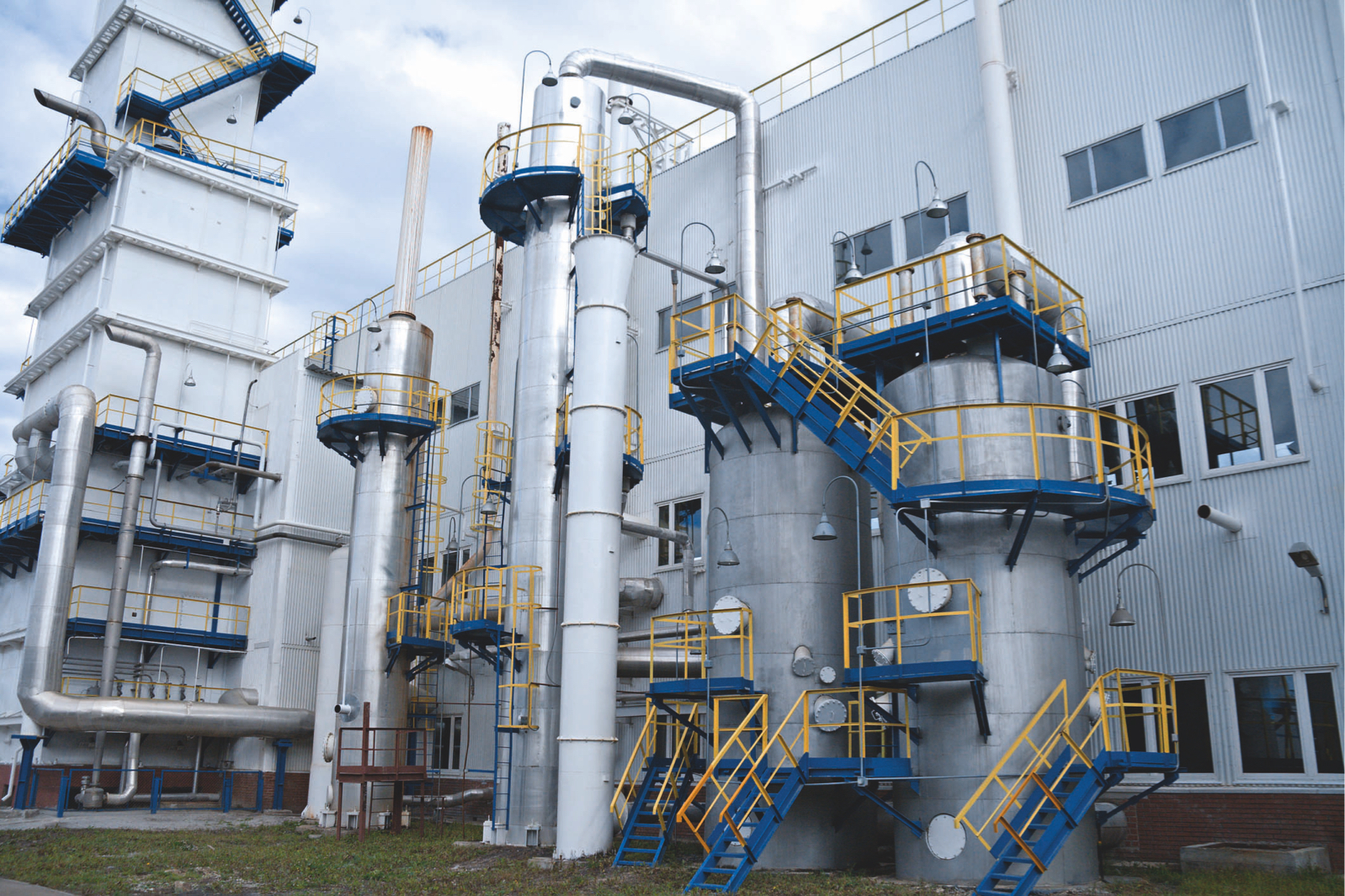
Smart heat recovery despite corrosive flue gases
Lubrizol in Farmsum (Groningen), a manufacturer of CPVC (thermoplastic), aimed to reduce the energy consumption of its drying processes. Two limiting factors stood in the way. The first was the high concentration of hydrochloric acid in the drying air. As the air cools below the water and acid dew points, hydrochloric acid forms, which can damage conventional heat exchangers. This challenge was overcome with a polymer air preheater that withstands corrosive flue gases.
The second limitation was the relatively low temperature of the flue gas—just 59 °C. However, thanks to a smart design, it was still possible to use this heat to preheat the incoming cold air to 56 °C. This resulted in a 170 kW reduction in energy use—without any corrosion issues.
Specifications
- Operating hours7,200 h/year
- Flue gas flow13.000 kg/h
- Flue gas temperature59 °C
- HCl concentration100 mg/Nm3
- Heat exchangerPolymer air preheater
- Recovered output170 kW
- Recovered energy4,406.4 GJ/year
- CO₂ reduction248 tons/year
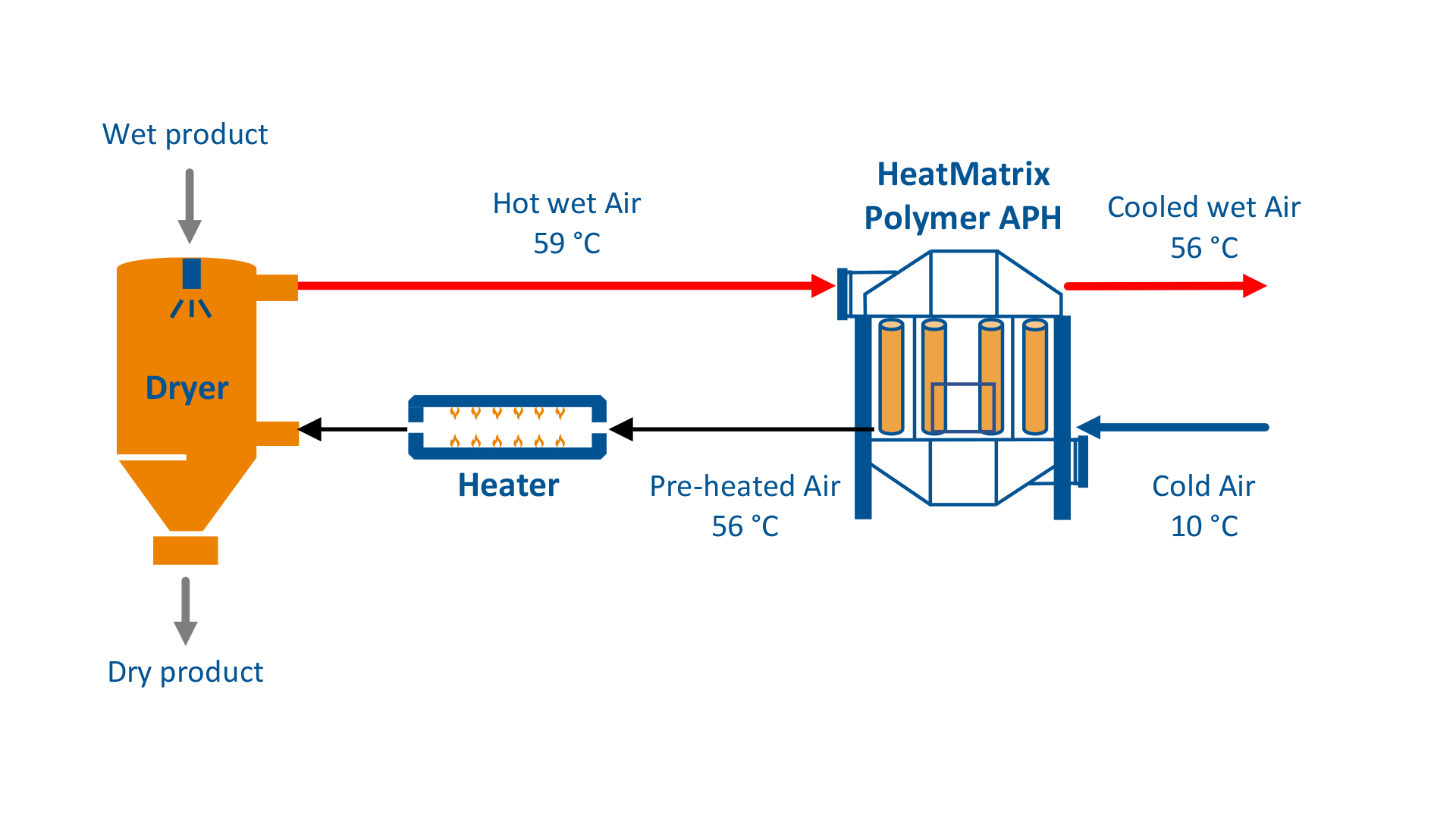
“The polymer air preheater from Heat Matrix has proven to be a robust solution. We have not encountered any corrosion issues. Since installation, the energy consumption of our dryer has been reduced by 8%.”
Henk Ruiter – senior Projectengineer, Lubrizol
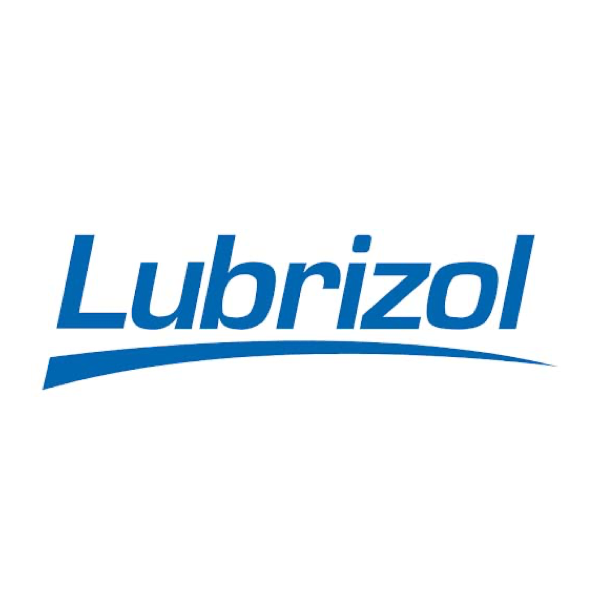
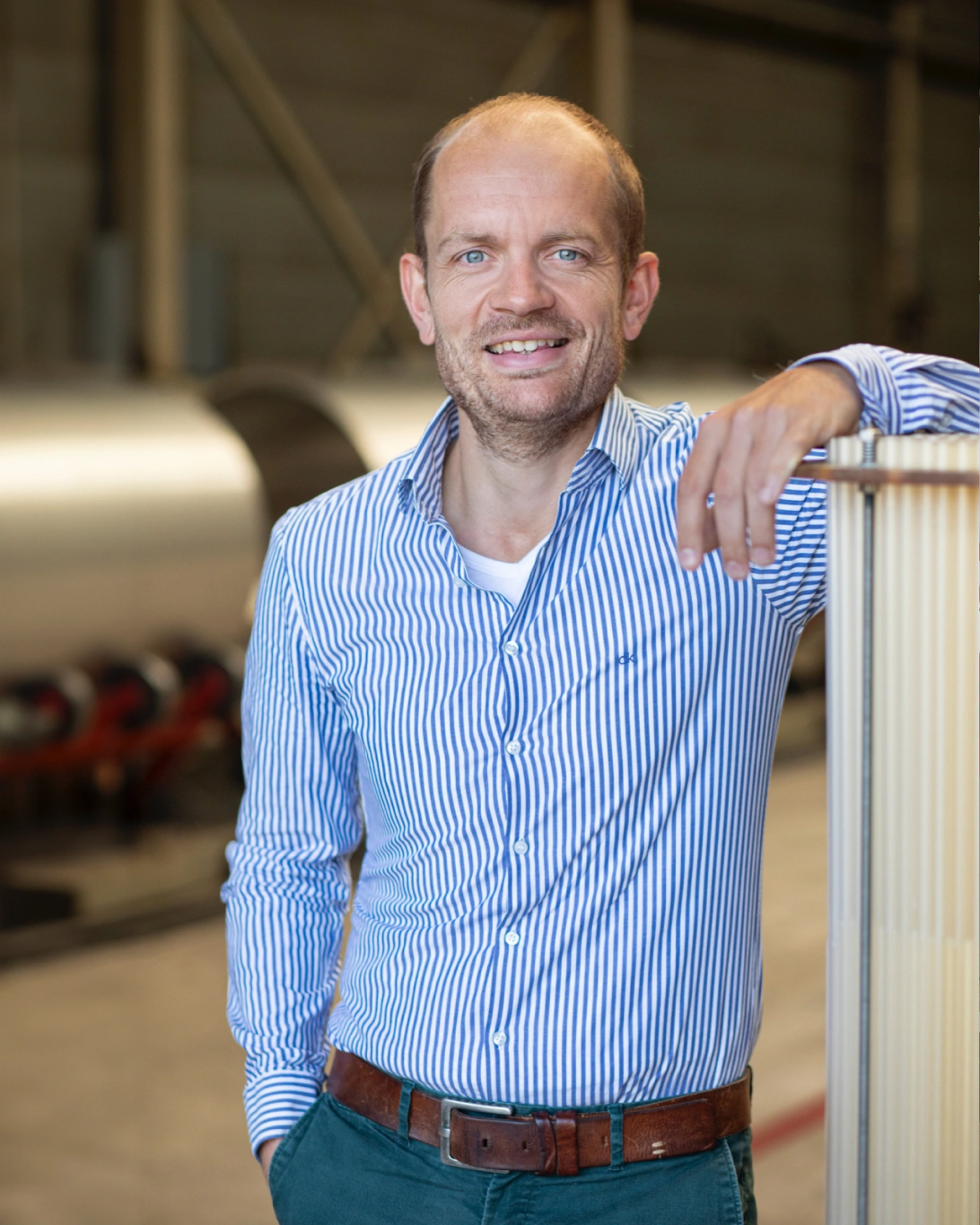
Contact
Curious about your savings potential?
A Heat Recovery Scan gives you quick insight into the most promising concepts for heat recovery, energy savings, reduction of CO2 emissions and payback period.
Related references